Custom Fittings Reduce Leak Points and Maintain System Integrity
Consider this little known fact: over 100 million gallons of hydraulic fluid are lost each year due to preventable leaks. So let’s look at the retail price of a 55 gallon drum of hydraulic oil from a well know online distributor: $850. At that cost, we are dumping $84.4 billion of hazardous waste each year. We say ‘dumping’ because we’re not only throwing away 85 billion dollars; we are leaking a tremendous amount of potentially toxic fluid. Chances are most of it is not being properly recycled or reclaimed. Instead, it ends up in the soil of construction sites or down the floor drain in manufacturing plants. And remember the operative word in the first sentence: preventable.
These are the hard costs. Now let’s consider the soft
(but very real) costs:
Maintenance
Downtime
EPA Fines
Or Worse:
A job site or plant is
shut-down for violations
More often than not, leaks are caused at the fitting threads or improper O-rings. Though hoses rupture and burst, frequent selection of the wrong fitting, over or under tightening and improper hose, tube & fitting assembly are the biggest culprits of hydraulic leaks. Threads that are not seated properly and O-rings that are not per specification cause unexpected leaks.
Since most hydraulic leaks are at the threaded connection, let’s look at some typical causes and ideas for prevention. After all, standard fittings are for standard connections in standard applications. And yes, there are many ‘standard’, worry free, applications. Yet most field engineers will tell you that ‘standard’ usually only happens in the lab, not in the field.
This is not only true in hydraulics. For instance, consider a compressed natural gas filling station. The gas runs underground from a compressor to a dispenser (the pump that fills the car or truck), often for many hundreds of feet. The only connectors are compression fittings at the end points of the tube because the NFPA (National Fire Prevention Association) code does not allow for mechanical fittings underground when running high-pressure gas.
The only choices underground are connecting multiple sticks of stainless tube with longitudinal welds, or running continuous lengths of seamless coiled tubing, connected at the ends with special compression tube fittings. Without the proper connections, natural gas will leak into the atmosphere.
It Starts With the Design

Fluid and gas conveyance goes well beyond picking a fitting, clamp, tube and hose that are matched in a catalog. A custom designed ‘special’ allows you to tailor the connection for your specific application, increasing reliability. A design engineer will likely begin by reducing the number of connections in the design of the system in order to reduce the number of potential leak points. The fewer the connections, the fewer opportunities for leaks. In many applications, custom designed fitting connections, developed for the specific pressures and environment, will provide the best possible leak-free system, and also the most efficient. However, too often field maintenance or improper installation can thwart the best design intentions. Using mismatched fittings, faulty or inferior O-rings or trying to fix a leak by adding more connections to the system only makes things worse. Keep in mind that a leaking hydraulic system doesn’t always mean poor performance. As long as pressure is maintained, the overall “system” may run fine. Just not efficiently.
It is a given that reputable fitting manufacturers offer products that meet SAE and ISO standards. However, selecting components that provide leak-free performance in every application is not an easy task. An assembly of fittings, hoses, pumps and cylinders may perform without a glitch in one application but leak like a sieve in another.
For instance, a cylinder that articulates the arm on an excavator may be designed to be leak-free and operate perfectly due to proper design of dampening with the equipment frame and long, flexible hose lengths. Yet the cylinder that operates the bucket may experience load shocks, pressure spikes and variable impacts resulting in multiple leak points. But today, new zero-leak designs give hydraulic fittings the greatest potential for controlling leakage.
Utilizing newer seal technologies, some manufacturers have developed fittings that stand up to the demand of the higher pressures that current hydraulic systems experience. They then take it ‘beyond the lab’ with techniques that ensure a leak-free connection when installed.

These companies have outpaced the industry by developing custom “leak-free” fittings. Yet many only carry a limited number of sizes and styles, and special designs are too expensive to consider for many applications. However, component manufacturers such as Brennan Industries carry a broad product line and have the engineering capabilities to make custom, leak-free fittings more the norm, than the special.
Focus on the Components
The variety of fitting options is impossible to count. Many industry experts suggest the large variety of mismatched fittings is a leading cause of leakage. Most large manufacturing plants and construction equipment operators stock dozens of fitting styles from numerous manufacturers in order to maintain multiple types of machines. So often one type of fitting is connected to what seems to be a similar fitting simply because they appear to fit, which invites leakage.
Selecting and properly installing the right fitting is imperative. Often a tapered metal-to-metal interface of the port and plug can tolerate adverse conditions such as vibration and frequent pressure variations without leaking. The design incorporates the engagement of the tapers to minimize any gaps. However, becoming familiar with the different types of custom components to use in a given application is essential in designing a leak-free system. By consulting with Brennan Industries’ Engineering Solutions Team, the system can be developed to ensure the right components
are used.
For instance, precisely engineered Port Connections that incorporate an elastomeric O-ring seal provide the best reliability. UNO, BSPP and SAE 4-bolt flange fittings are typically the first choice for leak-free connections. On the other hand, standard NPT fittings can be the least reliable in high-pressure hydraulic systems because the threads can allow a leak path when under higher pressures. When tightening an NPT fitting the threads become deformed to make the seal. Consequently, any additional loosening or tightening further deforms the threads which will increase the potential for leaks.
O-ring face seal (ORFS) fittings are becoming a more popular and reliable choice in hydraulic and tube connections. Well designed ORFS connections provide a seal that is highly reliable due to its elastomeric seal and is one of the best choices for a leak-free connection.
JIC 37-degree flare is the most common hydraulic hose connection. They are relatively inexpensive, easy to install, available in many sizes and easily adaptable from imperial to metric. Yet the standard metal-to-metal seal of the flare does not necessarily provide a reliable,
leak-free connection.

Flared connections have become prone to weeping in recent years due
to increasing hydraulic pressures in newer systems. Yet custom flare joints can be still be a great selection for leak-free connections when incorporating a conical washer between the JIC nose and flare and then applying a sealant to eliminate leakage at the connection. This is a good solution when the system is stationary and is suitable in cases where the JIC fitting needs to be frequently dismantled and reassembled. In the right applications, the combination of the conical washer and sealant ensure a leak-free connection and helps to protect the sealing faces from fretting, galling and overtightening.
System Design - Pressure & Temperature
The selection of standard or custom fittings in system design must take into account critical factors such as temperature, pressure, shock, vibration, environment, contamination, fluid velocities, size (OD & tube wall thickness) and the media being conveyed. The most critical of these considerations is pressure and temperature.
PRESSURE:
The system should be designed around the minimum and maximum operating pressure, including potential spikes in pressure. As is commonly understood, the fitting’s pressure rating must be equal to or greater than the system pressure. In most designs tube fittings are rated at a 4:1, applied as a ratio of the material strength to the dynamic pressure rating of the fitting. This 4:1 rating is typically used under normal conditions. Yet when the system will be experiencing conditions of severe vibrations and shock, operating a “de-rating factor” should be applied against the dynamic pressure of the fitting. The de-rating is used for designing the system at a factor less than its rated maximum capability as shown below:

TEMPERATURE:
In addition to designing for pressure rating, both ambient and fluid temperature must be calculated into the system design. Considerations should be given to temperature extremes and how they will affect the components and overall system operation. System operating temperature ranges are contingent on component material, plating and seals as shown below:

Matching Components in the Field
The most prominent fitting manufacturers offer thread ID kits and charts for easy identification of fittings and correct installation methods. Properly matching, torquing and assembling couplings is vital to maintaining hydraulic-system integrity. It’s possible that an improperly torqued coupling will not leak, yet other issues may still result. For instance a 37-degree fitting that has been over-tightened may deform, restricting flow and causing turbulence in the hydraulic fluid which can generate heat and decrease system performance. Over torquing will also strip threads and may crack the cone or seat, which can eventually cause leakage, especially if
pressure fluctuates.
All components should be inspected prior to assembly and while in service to help prevent leaks. Caterpillar’s Guidelines for Reusable Parts and Salvage Operations (Media Number SEBF8176-01) examines what parts can be reused and how to repair defected components. Often fittings with minor nicks or burrs can be reconditioned. But more serious damage to sealing surfaces, distorted face flanges, deformed stems or swivel nuts, welded parts or components subjected to high heat can cause serious damage to the system. It is best to not reuse fittings and other critical components whenever possible.
It is also recommended to not use couplings with different types of plating. Dissimilar plating may create the potential for vibration that will loosen the connection and cause leaks.
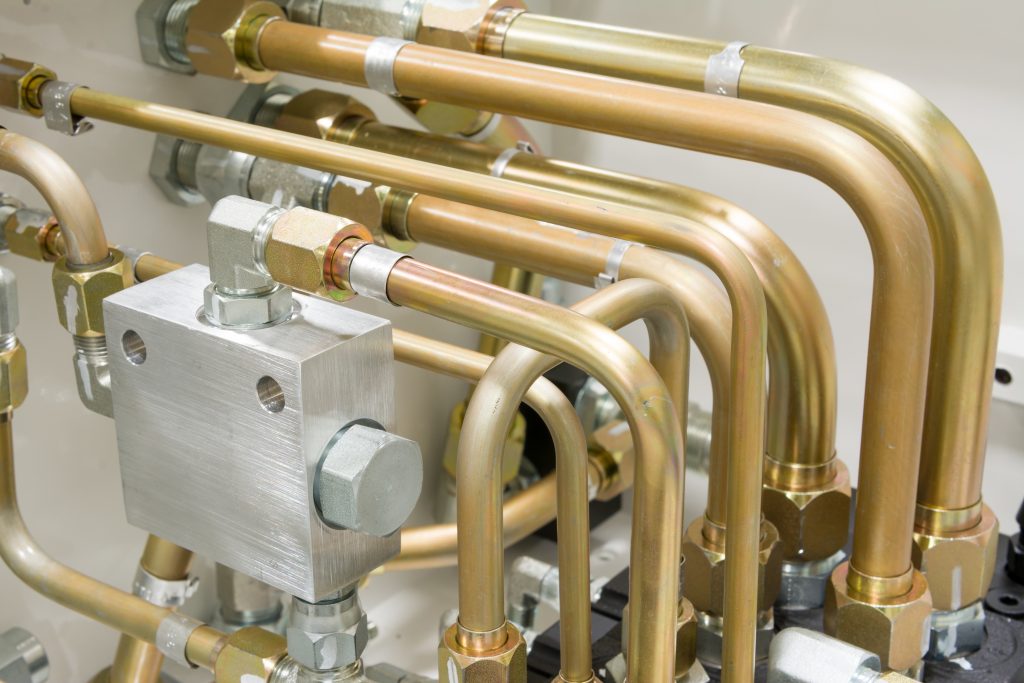
In addition, O-ring seals must be compatible with the type of hydraulic fluid being used; otherwise the seal may deteriorate due to an unforeseen chemical reaction.
The best way to avoid component compatibility issues is to use parts from a single manufacturer. Do not mix and match brands. Instead design engineers and field technicians should look at the system as a whole, rather than as individual pieces, so that the entire system is compatible in order to maintain performance and extended service life.
Consider the Importance
As appropriately described in the Harvard Business Review, when an airline orders an engine from Rolls-Royce or GE they are not looking for a “piece of machinery”, they need a powerful, safe, and reliable means to deliver air passengers to their destinations. There are many critical systems and components in the design of the engine. One of the most important is the hydraulic system. Designing the hydraulics with custom leak-free fittings is imperative. Consider the potential effects of failure from “standard” hydraulic components in the system design of an aircraft:
• Difficulties with landing gear extension
• Collateral damage to systems due to a ruptured hydraulic pipe
• Inability to activate thrust reversers
• Inability to extend/retract high lift devices such as flaps or slats
• Inability to retract landing gear
• Loss of anti-skid systems
• Loss of autopilot
• Loss of low visibility landing capability due to degraded autopilot or flight controls
• Loss of nose-wheel steering
• Partial or complete loss of control over adverse surfaces
• Possible loss of ETOPS and/or RVSM capability
• Reduced braking capability upon landing
Conclusion
Brennan Industries’ Engineering Solutions Team provides customers with customized solutions for their specific system needs. They have a dedicated staff that focuses on solutions tailored to the most unique highly engineered critical flow components. Because Brennan controls the manufacturing process from end-to-end they offer the widest variety of sizes, materials, plating, coatings, and customized solutions.
Whether it’s altering a standard product or starting from scratch,
the Brennan Engineered Solutions Team has the expertise and reputation to provide the best solutions for fluid system design.
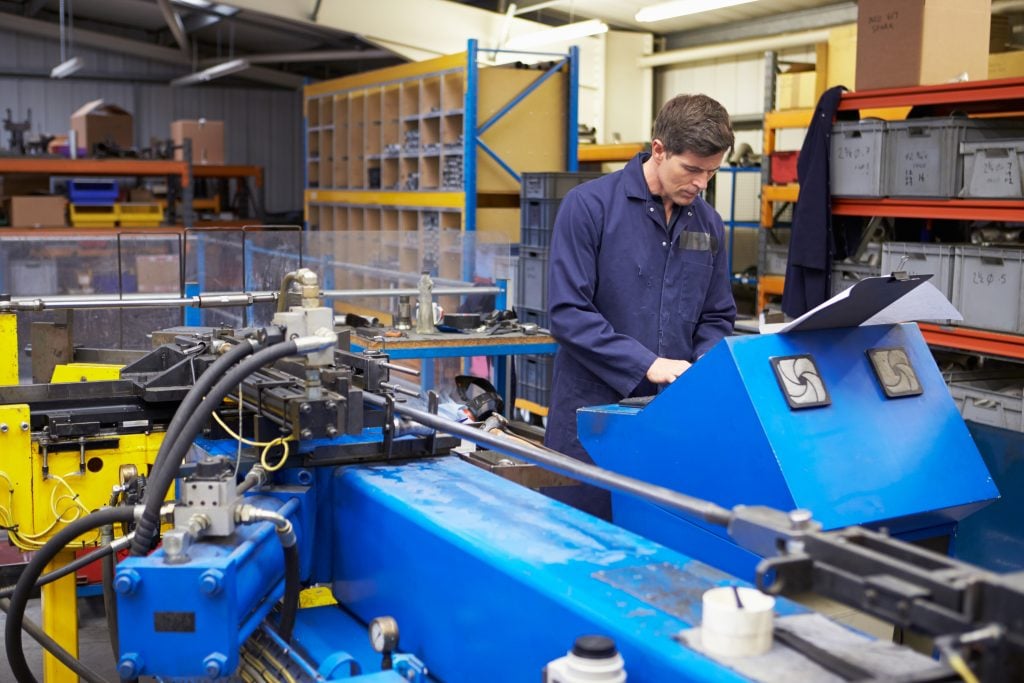
Brennan is also AS9100C and NADCAP certified. They have a broad line of fittings approved for use in Civilian and Defense aerospace applications. This ensures Brennan maintains the highest manufacturing standards in fluid connections, making them the specified choice of many construction, industrial and commercial equipment manufacturers for better performance and service life.
SOURCES:
Construction Equipment®
Hydraulics & Pneumatics
Machinery Lubrication Magazine
Harvard Business Review