
Introduction to the Metals Used in the Manufacturing of Fittings
Hydraulic and instrumentation fittings must have the necessary strength to withstand the often high pressures and temperatures of the system. The fittings must also resist the potential of corrosion and rust from the different media inside the system and the outside environmental conditions. Generally, metal fittings are used in most hydraulic and instrumentation systems due to their high pressure requirements or corrosive conditions. Though plastics typically have a higher resistance to corrosion than metals, their comparatively low strength and durability make them less suitable for hydraulic systems and the majority of instrumentation applications.
Metal fittings are primarily made of carbon steel, stainless steel, other exotic alloys (i.e. Hastelloy®, Inconel® & Monel®) or sometimes brass. For the purposes of this paper we are focusing on carbon
and stainless.
These metals are strong and durable, and can withstand high pressures and have exceptional heat resistance. Carbon steel fittings can withstand temperatures from -54°C (-65.2°F) to 260°C (500°F) and are an alloy of iron, carbon other metals for high strength and durability.
Stainless steel has superior resistance to chemicals and corrosive environments. Stainless steel fittings withstand a typical temperature range from -254°C (-425.2°F) to 649°C (1200.2°F) and possess excellent corrosion resistance properties. Therefore, the characteristics of stainless make it a highly suitable fitting material for applications where the internal fluid or external environment is subjected to extreme heat and/or corrosive conditions.
It is also the necessary choice for high pressures, as stainless steel fittings are typically rated to 10,000 PSI and specially developed stainless fittings can withstand pressures up to as much as 20,000 PSI.
The Best Methods for Manufacturing Steel Fittings
Forged fittings are far superior to other processes in the majority of applications. The forging process provides consistency in the structure and composition of the materials, and the metallurgical recrystalisation and grain refinement strengthens steel products, particularly for shear, impact and strength.
Forged steel is stronger and more reliable than brazing, casting and plate steel because the grain structure of the steel is altered, conforming to the shape of the part.
SOME OF THE LEADING ADVANTAGES OF FORGED FITTINGS INCLUDE:
• The tight grain structure makes them mechanically stronger than alternative methods
• Low cost due to less waste of excess flashing and ability to produce near-net shapes
• Exclusion of porosity, cavities, shrinkage and cold pour issues
• Less need for expensive alloys to manufacture high strength components
• Greater wear resistance and longer service life of the fitting
• Does not require a special skilled operator to produce
• Wider variety of solid body shapes can be produced
• Superior ability to withstand impact over brazed or casted fittings
Forged Fittings VS Brazed: The Difference
FORGED FITTINGS
Forged fittings are made from one piece of metal, which allows them to be produced with less material providing a more compact design and smaller wrench flat. Most forged fittings are made using a hot forging process which heats the metal above its recrystallization temperature, providing for the annealing process to obtain growth of new grains in the metal without phase change.
In other words, hot forging is a metal shaping process which takes a malleable metal part, such as a billet or other metal workpiece and heats up to about 75% of its melting temperature. It is then worked, or essentially molded, to a predetermined shape in a die.
BRAZED FITTINGS

Brazed fittings are made from multiple, pre-machined components that are combined together, resulting in a finished part. Though the brazing process can allow for fittings with some customization when combining multiple components, they are susceptible to fatigue at the joints. Most brazed fittings are made by furnace brazing, which can generate a large number of parts on a continuous belt in a controlled heat cycle and atmosphere.
However, extra steps such as ensuring very close fits are necessary to facilitate the capillary action in the brazing process and secondary component parts are annealed during the process. In addition, provisions must be made in the design process for the location and fit of the brazed components.
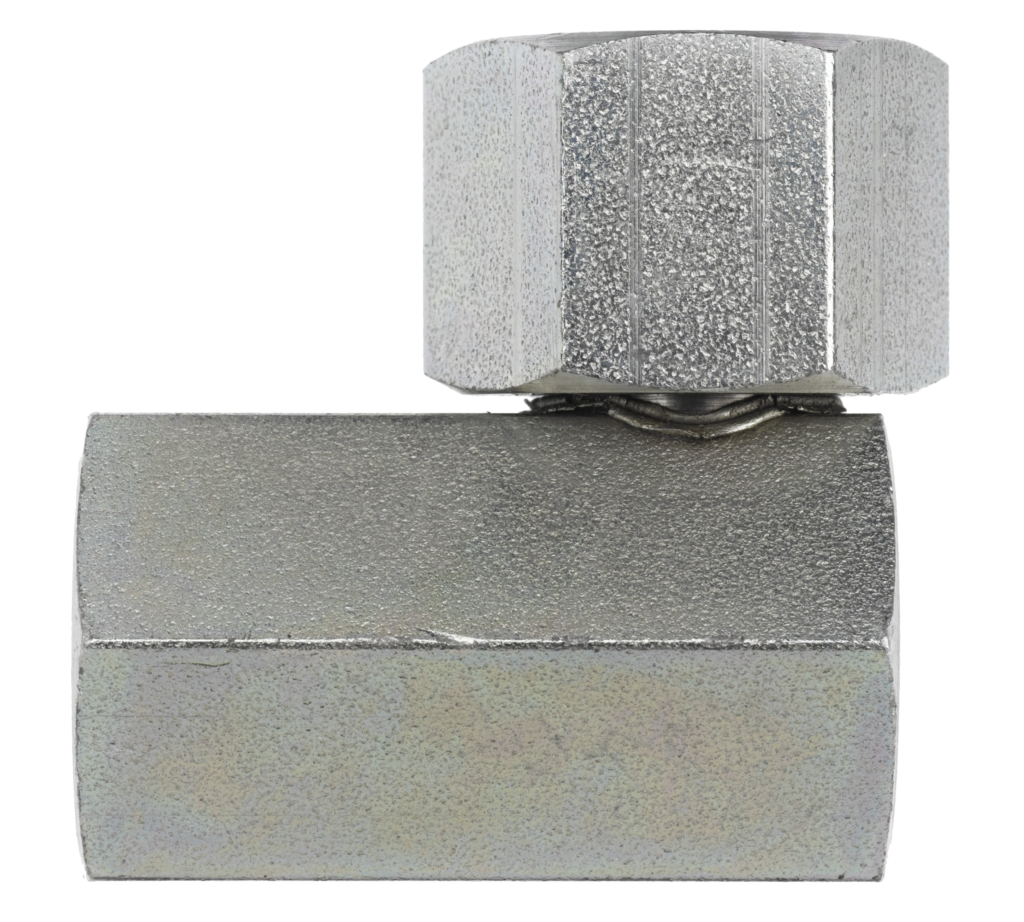
Why Choose Forged Over Brazed Fittings?
Producing forged steel fittings includes cutting and heating billets, then using a pre-formed die that creates the desired shape under high pressure on the heated billet. The part is then trimmed and shot blasted to remove any flashing. This process produces a machined forged blank fitting to exacting net shapes and dimensions.
Forged steel fittings are primarily threaded or socket weld end connections. Forged threaded fittings conform to ASME B1.20.1 and socket weld fittings conform to ASME B16.11.
COMMON MATERIALS FOR CREATING FORGED FITTINGS
- Carbon Steel: for forged carbon steel piping connections
- Stainless Steel: 304 or 316 stainless steel for corrosive environments and high pressure applications
FITTINGS ARE CATEGORIZED IN TWO BASIC GEOMETRIC CATEGORIES: STRAIGHTS AND SHAPES
- Straights are normally machined from cold drawn hexagonal or round bar stock
- Shapes are typically forged as described above into one solid piece. Because forged fittings are a single-piece they are no potential leak paths. On the other hand, a brazed fitting made of two or more pieces “brazed together” allows for cracks or other potential leak paths. In addition, due to its single body construction a forged fitting is much stronger because it does not have a secondary brazed joint. The advantage of a forged piece clearly allows for higher-pressure ratings and a longer service life than a brazed fitting.
In the secondary operation, whether straight or shaped (i.e. elbows, tees, etc.) the orifice of the forged piece is then drilled out to the exact ID specification. If it is a threaded fitting the threads are cut to specification. If a socket weld fitting, the forged part serves as the outer body and the ID is drilled
to specification.
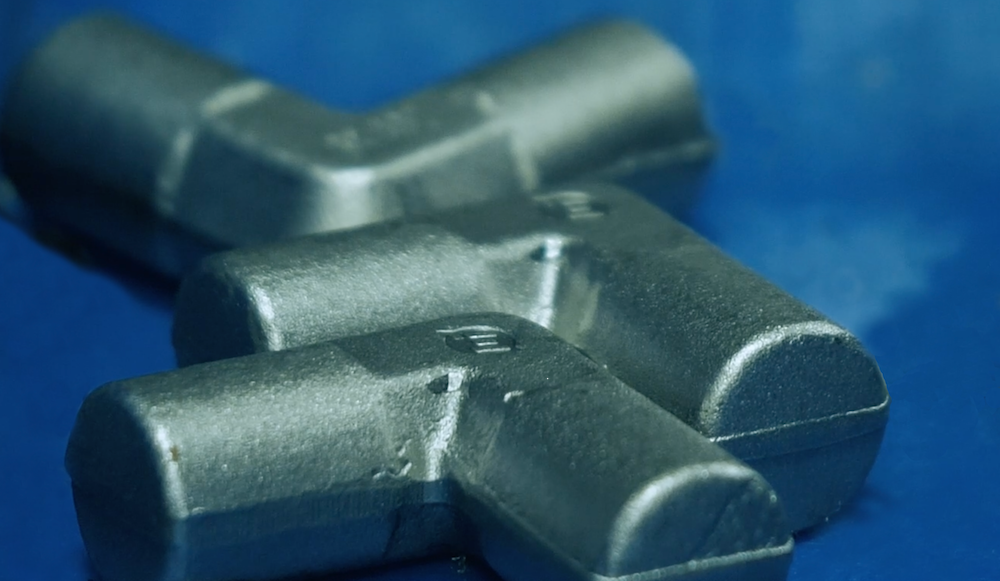
Advantages of Forged Fittings VS Other Processes
FORGED FITTINGS VERSUS CASTING
A cast fitting is made by pouring molten metal into a mold of the desired shape. Forged steel is stronger and more reliable than castings because the grain flow of the solid steel piece is altered to conform to the shape of the part in the die. Because of this, forging provides a uniformity of the structure and composition of the finished part. The refinement that occurs is due to the thermal cycle and deformation process which is what strengthens the final part in respect to internal working pressure, and external impact and shear strength.
ADVANTAGES OF FORGING OVER CASTING
• Due to the tight grain structure, a forging is mechanically stronger than a casting
• Unlike castings, forgings are not susceptible to cavities, cold pour problems, porosity or shrinkage
• Castings typically require more expensive alloys to achieve the high strength required for most fittings
• The tight grain structure of forgings provides more wear resistance and is not so hard as to be more likely to become brittle in comparison to castings, allowing the forged fitting to withstand higher pressures, more extreme conditions and experience a longer service life than a casted fitting.
Testing performed on a blank HRC 38-42 forged grinder insert wear/wash is about the same as on a high alloy HRC 46-50 cast grinder insert, however a HRC 46-50 casting does not have the ductility to handle high impact grinding. This testing illustrates how forged fittings will withstand higher impacts, pressures and wear resistance than casted fittings. In short, forged metal fittings have a longer and more reliable service life than castings, and are typically less expensive in the identical application.
Conclusion
The structural integrity of the forging process provides the highest strength possible to a part. It produces a solid structure that is free of internal defects which can reduce the durability and strength of the metal. The forging process provides the highest strength to weight ratio of any metal forming process. Forged fittings are the best choice for critical applications that require high pressure, high temperature, exceptional wear resistance and internal toughness.
Forged fittings are made in what is called a closed die process (a.k.a. hot drop forging), also known as impression die forging. This process is commonly used in the manufacturing of small or medium metal components using a plastic deformation method. Unlike in the open die forging, the material is forced to flow in a pre-machined closed die of the specified shape. Close die forging provides near-net shapes to attain more complex geometries that are very close to the dimensions of the finished part. The plastic deformation is a process of rapid shots which forces the material to fill the shape of the die. The final product is considered a flashless forging that chucks on the OD of the part without having to worry about a parting/trim line. The result is less waste, stronger part integrity and a more concentric finished part.
SOURCES:
ATC GROUP
Boss Industrial
CFS Forge
Club Technical Mechanical Engineering
Hydraulics & Pneumatics
ScienceDirect
Viking Forge