Connection Type: Instrumentation Needle Valve
What are Instrumentation Needle Valves?
Instrumentation needle valves are widely used in process measurement and control systems in food & beverage, medical equipment, transportation, chemical processing, water treatment and oil & gas industries. Popular needle valve designs are available in stainless steel and brass, and incorporate PTFE gland packing for it’s outstanding resistance to chemical attack, low coefficient of friction and wide temperature tolerance. Instrumentation needle valves are available with screwed bonnet or integral bonnet. Brass instrumentation needle valves are rated for pressures up to 3,000 PSI and temperatures to 350°F, while stainless steel instrumentation ball valves are rated for pressures up to 6,000 PSI and 450°F.
A Needle Valve uses a precision engineered tapered pin to gradually open a space for fine control of flow. The flow can be controlled and regulated with the use of the needle. A needle valve has a relatively small orifice with a long, tapered seat, and a needle-shaped plunger on the end of a screw, which precisely fits the seat for valve shut-off. When the needle valve screw is turned the plunger retracts allowing flow between the seat and the plunger. However, precise regulation of the flow rate can be controlled when the plunger is completely retracted. Needle valves are often used in vacuum systems where precise control of gas flow at low pressure is required. They are often used as component parts of other, more complicated valves systems.
Advantages of Using Instrumentation Needle Valves:
- Readily available and offer a large variety of sizes, shapes, combinations and materials
- Ability to accurately control the rate of flow makes this design extremely flexible
- Highly precise yielding increased efficiency and increased safety
- The stainless steel needle valves are corrosion free and leak proof in high temperature and high pressure applications
Disadvantages of Using Instrumentation Needle Valves:
- The design prevents visual determination of valves open or closed position
- They experience pressure loss do to the heightened restriction of fluid flow
- The seat and the needle could be damaged with suspended solids present in fluid
- The seat of the needle valve could be damaged due to excessive turning force while closing the valve
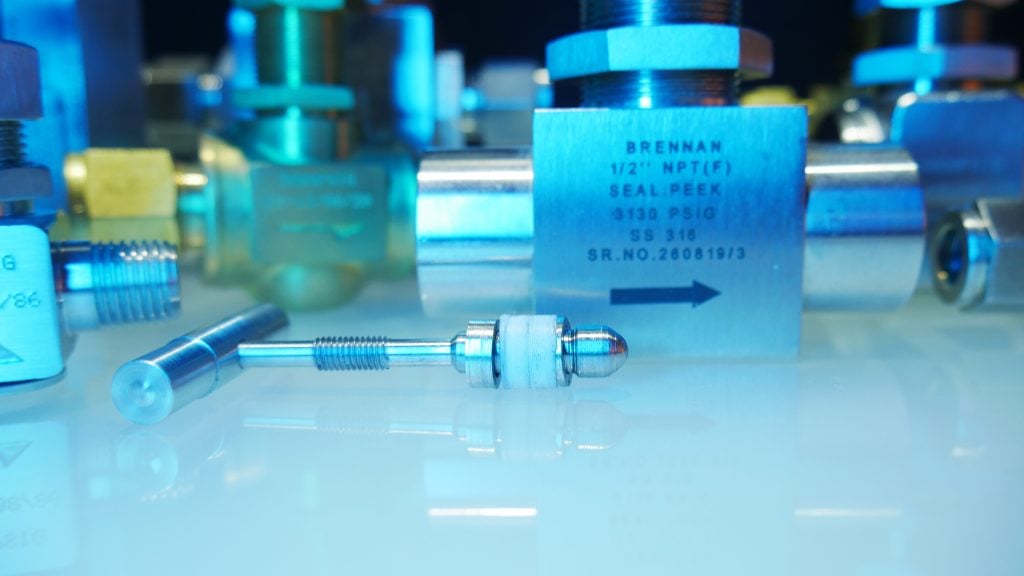