Understanding Hydraulic Fluid Contamination
Hydraulic fluid acts as the lubricant between moving parts and often the necessary resistance in components, such as brakes or power steering. The most common applications which require regular monitoring of fluid contamination are in heavy equipment that are exposed to the environment such as off-road earth moving equipment and farming equipment.
Industrial machinery that experiences frequent actuation
or movement is also more susceptible to contamination than equipment that has infrequent
actuation, or is isolated to a clean environment.
Contamination control is integral to ensuring efficient operation of a hydraulic system by identifying and measuring potential types of contamination. Taking the proper steps will extend the service life of hydraulic equipment.
Hydraulic systems are integral parts of a variety of equipment, including:
Aircraft Flight Control Systems
Backhoes
Excavators
Garbage Trucks
Hydraulic Brakes
Industrial Machinery
Lifts
Power Steering Systems
Transmissions
Hydraulic fluids are individually formulated for specific applications. They are usually comprised of a base stock and an additive package. The additive package consists of chemical compounds designed to protect the base stock, which is primarily made up of natural mineral oil-based fluids. It is essential to have the correct formulation of fluid for the proper performance of the system. Many additives include anti-corrosion, antioxidants, anti-foaming, anti-wear, viscosity-index improvers and certain extreme pressure (EP) agents.
Water and any foreign particulates will contaminate and adversely affect the chemical properties of the additives and the base stock of hydraulics. The presence of contamination can cause excessive wear on the system or premature failure, sometimes with catastrophic consequences. Imagine an aircraft control system seizing up due to contaminated hydraulic fluid. This is why critical hydraulic systems should be regularly tested of contaminants and variations in pressure.
Hydraulic Fluid Contamination Testing
To avoid contamination of hydraulic fluid it is important to place filters at regular intervals in the hydraulic system to collect contaminant that may inadvertently get into the line.
For certain equipment that is more sensitive or regularly exposed to dirty environments, contamination control procedures should be put into place for periodic testing of the cleanliness of the hydraulic fluid, usually based on the equipment manufacturer’s recommendation.
The fluid should also be tested after equipment maintenance that may subject the hydraulic system to outside elements. Fluid testing should be conducted after new fluid is added, new components are placed in line and replacement of hoses or any other condition that exposes the current fluid. Purging a system from the existing fluid and replacing it with new is a critical time to have the system tested due to exposure to the outside elements and to ensure the new fluid is not contaminated. Suppliers of hydraulic fluids recommend chemically analyzing the fluid on a regular basis to be proactive in eliminating problems before they occur.
The most practical method for regularly testing fluid line systems is to place test point fittings at regular intervals throughout the system which allows sampling at working pressure without disrupting the system’s operation and avoiding costly shutdowns. Quality test point connections are leak-proof before the ball check is open to minimize contamination and their self-locking metal cap helps protect the system. It is recommended to have a full line of test point components on hand, or a variety of test point kits which include all styles of connections, test hoses, couplings, pressure gages, gage adapters, plugs and probes. These kits provide all of the components necessary for periodic testing of a wide variety of equipment from different manufacturers.
MRO - Understanding the Proper Maintenance Techniques of a Hydraulic System
Preventative Maintenance
Preventative maintenance of a hydraulic system is crucial for maintaining the life of the equipment.
- Establish a method for following the manufacturer’s recommended maintenance schedule.
- Determine the frequency and extent of maintenance based on the equipment’s working environment.
- Ensure the maintenance schedule includes what the manufacturer recommends regarding the hydraulic fluid’s ISO particulate and the proper method for extracting fluid samples from the lines of the operating system.
- Take into consideration the filter manufacturer’s requirements and stated limits.
- Extract fluid samples from a main flowline ensuring the particulates in the samples are representative of the fluid flowing through the line. As stated above, this is accomplished by having test points at regular intervals throughout the system.
Regular standards and procedures should be documented and adhered to for the proper maintenance of any equipment with a hydraulic system. Preventative maintenance is the most important function to maintaining the service life of the equipment and reducing costs associated with equipment or component replacement, or unwanted shutdown.
Corrective Maintenance
Corrective maintenance is the repair or replacement of components in the system. Typically corrective maintenance is the result of component inspection during preventative maintenance and addressing the anticipated issue before failure occurs. Ideally the need for corrective maintenance can be identified and addressed in preparation for a scheduled or planned shutdown.
After corrective maintenance it is important to inspect the component to identify the reason for the anticipated or actual failure. This information should then be used in the preventative maintenance schedule to eliminate having the issue occur in the future.
Test Point Plugs - Monitoring Hydraulic System Conditions Without System Shutdown
As indicated above, pre-installed test points are critical tools for monitoring the condition of a hydraulic system. These test points incorporate quick-connect couplings for easy access along the system while it is in-service and are used to identify problems before they occur.
For operations with a variety of equipment from multiple manufacturers it is best to have preassembled test pressure monitoring kits with
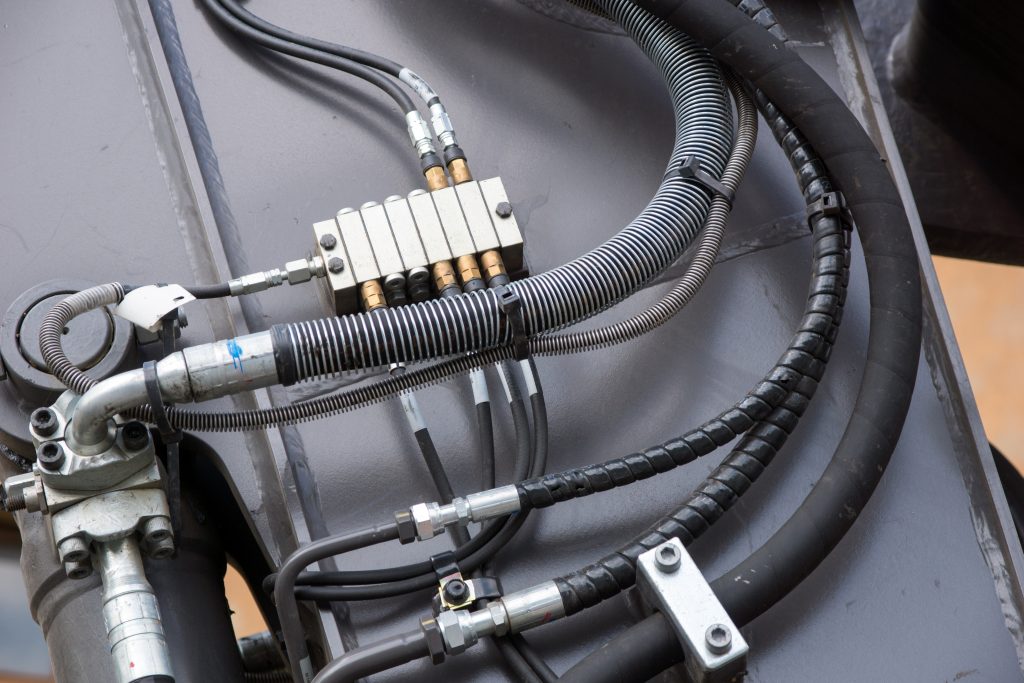
assortments of popular components on hand at all times. These kits are available with everything required for instant pressure checking regardless of style of the OEM’s existing hydraulic systems.
It is important to reiterate that quick-connect couplings allow for monitoring and controlling pressure, venting a system or drawing samples under working pressures. They are ideal for hydraulic oils and other mineral-based fluids used in off-road mobile equipment and other hydraulic systems in manufacturing environments. These test point fittings connect easily to measurement, control and switching devices to allow for quick and easy system testing.
Quality & Contamination Control - How to Monitor & Avoid the Effects of Contamination in Hydraulic Fluids & Systems
Up to three-quarters of hydraulic systems fail due to contaminated or old hydraulic fluid. Though contaminants in a hydraulic system can be solid particles or liquids, water is a major cause for concern. While solid particles contaminate the system by chemically reacting with the fluid, water contamination varies from system to system. Water can form during the blend of the fluid, or it may be floating on the surface or settling to the bottom of the hydraulic fluid depending on its density. As expected, having water in the system usually causes corrosion of components and further contamination from corrosive by-products. Water can get into the system because of design flaws, the service environment, poorly controlled maintenance or other equipment servicing.
Primary Considerations for Contamination Control
Proper contamination control requires diagnostics and treatment of the hydraulic system. Diagnostics, often called ‘Condition Monitoring’, is the measurement and identification of the condition of the hydraulic fluid and system components for preventative maintenance. Proper preventative maintenance procedures and fluid monitoring are performed to establish fluid replacement schedules and maintenance protocols that are pro-active instead of reactive.
Diagnostics/Condition Monitoring is Integral to:
- Maintaining continuous production
- Avoiding potential damage to system components
- Reducing unplanned downtime
Cleaner fluid is the key to longer component life and increased uptime. The result is more reliable equipment that reduces maintenance hours and costly repair or replacement of components.
In manufacturing plants equipment is more isolated from the elements, yet contaminants cause 60% to 70% of all hydraulic component failures. However, with earthmoving equipment failure from contaminants can be as high as 85% to 90% if not properly maintained.
Heavy equipment used in construction is far more susceptible to moisture and particles than in
most manufacturing settings. This exposure can be very destructive to expensive components and equipment, not to mention the downtime that will negatively affect the bottom line. If particles get into an engine or other critical and expensive parts it can reduce the service life by 60% to 75%. While most operators know water, dirt and dust particles can harm equipment, they do not always appreciate the significant damage and downtime they will cause.
It is usually not just the visible dirt that causes problems. More often it is unseen silt particles as small as 1 to 5 microns. A study performed by Cummins Engine, identified particles smaller than 10 microns caused wear rates three to four times greater than those caused by 20 micron particles and larger. In addition, studies conclude that the abrasive wear on parts generate particles that can be extremely difficult to control unless proper preventative maintenance is routinely conducted.
Contaminative particles and moisture typically invade equipment through seals and air breathers. The air intake on the engine of construction equipment can allow over 95% of contamination. Air filters and manifolds are the first line of defense and should be effectively maintained. However the most stringent efforts may not stop silt-sized particles from entering through air filters. It is a little known fact that for every gallon of fuel used, as much as 10,000 gallons of air enters the engine through filters.
An engine in these environments can experience significant damage once a particle enters. Though current synthetic oil blends are designed to prevent soot and other contaminant accumulation, even the best full-flow oil filter may not prevent as much as one billion 5 micron particles from entering the system. This is because most full-flow filters are not able to capture particles below 8 to 10 microns.
Consider These Solutions
Supplemental Bypass Filter
By installing a supplemental bypass filter after the full-flow filter 5% to 10% of the fluid will be directed through an ultra-fine depth media filter of 1-3 microns. Bypass filtration has been shown to improve engine fluid cleanliness by as much 1/3 to over 1/2 in some cases. The proper use of a supplemental bypass filter has been known to double or even quadruple an engine rebuild service life. Some cases have shown to provide more than an additional 50,000 operating hours when using a supplemental bypass filter.
Frequent contaminants in off-road equipment are particles and moisture entering the system through the air breather, fill port or rod/cylinder wiper seals. This is easily avoided by using rod boots. These bellows covering the outside of the cylinder expand and contract as the rod moves in and out. In the past, typical boot materials did not hold up to the environment of construction equipment. However, today boots made of Kevlar or similar materials are far more suited to these harsh environments.
Desiccating Breathers
No less important than a bypass filter are the air breathers. A desiccant air breather replaces the standard dust cap or OEM breather cap. This provides better filtration to protect against extremely small particulates. These breathers contain layered desiccant filter elements which remove particulate as air is pulled through the breather while simultaneously blocking harmful moisture.

For instance, when a rod extends out of the cylinder the amount of hydraulic fluid required to extend the arm is replaced by air that enters through the tank breathers. The majority of tank breathers are not adequate for preventing silt sized particles (1 to 10 micron) from entering the systems and do not block moister. To block particles and moisture from entering through the breather air vents, fill ports should be replaced by high efficiency desiccating breathers. Most desiccant breathers remove moisture with a silica gel and incorporate a 1 micron particle removal element.
Preventing Corrosion of Hydraulic Systems
Beyond what has already been covered about keeping water and solid contaminants out of a hydraulic system, another step to help prevent corrosion is the use of rust inhibitors in the hydraulic fluid. These rust inhibitors place protective films on metal parts. Typically these films are water resistant and prevent rust from settling on parts. Certain additives that are hydrolytically stable in the presence of water are also used in the system. These additives help to avoid fluid breakdown and the formation of acid causing corrosion.
Equipment Uptime Impacts the Bottom Line
Using boots and correct breathers are important steps for hydraulic systems, particularly in construction environments. Yet contamination can still be a concern. Though full-flow filters play an important role, they may not be sufficient in some situations. In some cases bypass filtration systems should be considered if the environment is particularly dirty.
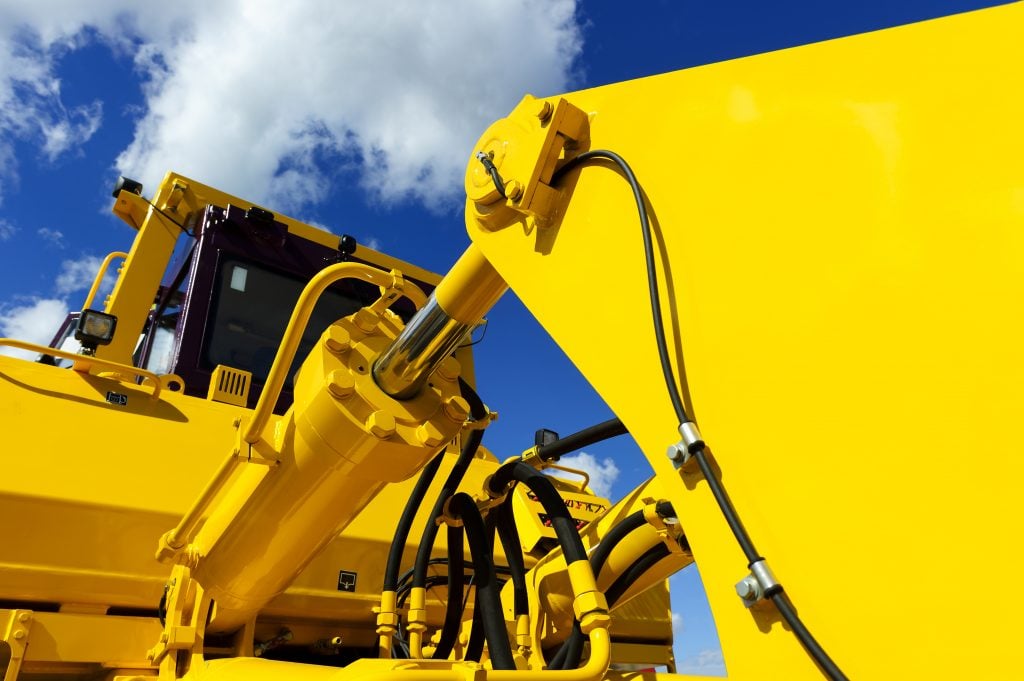
These preventative maintenance steps can make a huge impact on maintenance costs, equipment uptime and overall profitability of the job.
Important Steps to Ongoing Hydraulic System Care & Maintenance
System Care
Hydraulic fluid lines are the arteries of the hydraulic system. The fluids may be typical petroleum based mineral oils, synthetic fluids, fire-resistant fluids or special biodegradable fluids.
There are four primary considerations when it comes to the fluid to ensure the optimal service life of a
hydraulic system:
System Care
Most hydraulic system temperatures range from 110 to 150°F. There are some specialty hydraulic fluids that can operate at temperatures up to 250°F.
System Cleanliness
Even new systems can have contamination in the lines. Therefore it is critical to clean a new system before putting it into service in order to prevent contamination from the beginning.
Fluid Cleanliness
Even new fluid can easily become contaminated. It is important to store new fluids in an isolated clean environment in dedicated containers. In systems considered critical use quick disconnect fittings and hoses, and be sure to filter all oil added to the reservoir through a 5 micron filter.
Have a Standardized Oil Analysis Program
Be sure to follow the OEM’s specifications for how often hydraulic oils should be drained. And do regular system monitoring with test point fittings and gauges to allow for accurate examination of the system.
System Maintenance
Some manufacturers recommend a 10 Point Check of a hydraulic system as part of the regular
preventative monitoring:
1. Inspect filters, fill screens and breather caps
2. Check fluid levels. If adding oil, do not mix with other oils. It is essential to use the same brand of oil and equal viscosity grade the system is currently running
3. Check system temperature, ideally with built-in thermometers. You can also use hand- held infrared detectors if they are on hand. Again, follow the OEM recommendations for temperature range. If the temperatures are above the limit, check the cooler operation and settings of the relief valves.
4. Check pressure differential gages or filter indicators, or both.
5. Visually inspect the inside of the reservoir for signs of aeration (via the fill hole using a flashlight). Aeration is a condition in which discrete bubbles of air are carried along in the stream of oil as it enters the pump. Visual signs of aeration in the reservoir are generally foaming and/or little whirlpools taking small gulps of air into the suction strainer. Aeration can be caused by a variety of situations, one primary cause is accidental ingesting of air. If the pump is taking on air, the system will sound like gargling stones.
6. Visually inspect pipes, hoses and pipe connections for leaks or cracks. Leaking of hydraulic is not uncommon. Without maintaining proper fluid levels a system can overheat and cause permanent damage.
7. Listen for potential cavitation in the pumps (the formation of bubbles in the fluid). This can happen when air is released from the hydraulic oil when there is depressurization at the pump suction. It can then implode on metal surfaces when discharging. Should this happen the pump will give a high-pitched type whining noise. If it is not stopped immediately it can permanently damage the pump. The installation of a vacuum gage on the suction side of the pump with equalized pressure, as detailed by the pump manufacturer, can alleviate this catastrophic problem.
8. Check servo valves with an infrared thermometer. If the temperature is over 150°F, the valve is likely sticking.
9. Use an infrared thermometer to check the rotor bearing temperatures and hot spots in electric motors.
10. Take a small sample of fluid and inspect it for color, odor and any indication of contamination. Though visual inspections are limited and will only identify excess contamination, it is still a very important step.
CONCLUSION:
Preventative Maintenance Reduces Failure of Hydraulic Systems and Provides Significant ROI
As we’ve discussed, optimum preventative maintenance starts with quality test point fittings
and components that provide leak-proof

connections before the ball check is open to minimize contamination and have self-locking metal caps to protect the system. Having test points installed along the hydraulic system lines allows for regular, quick and accurate testing of system pressure and other variables critical to the health of the system.
Regular monitoring of system performance, analysis of fluid and scheduled fluid changeover are the keys to a long service life of equipment and components. Otherwise, there will likely be unplanned or even frequent equipment shut-downs that are far more costly than the required maintenance tools and a regular maintenance schedule.
Keep a variety of test point kits on hand that include all styles of connections, test hoses, couplings, pressure gages, gage adapters, plugs and probes required for the various off-road or industrial equipment you have in service.
SOURCES:
Design World
Engineers Edge
Equipment World
ForConstructonPros.com
Hydraulics & Pneumatics 6430
Hydraulics & Pneumatics 6436
Hydraulics & Pneumatics-test-point-fittings-1
IDCON, Inc.
International Organization for Standardization Machinery Lubrication
Mobil Industrial Lubricants
Reliabilityweb.com
The Heavy Duty Manufacturers Association
The Society of Tribologists and Lubrication Engineers (STLE)