Push to Connect Saves Time and Money
When it comes to low pressure instrumentation and plumbing applications of many kinds, saving time and ease of installation are the prime reasons for using Push to Connect fittings. These couplings are referred to in many ways; Push to Connect, push-to-pull, push-in, push-fit, quick-release and instant fittings are common names for a type of connection that is an
easily removed fitting which allows an air, gas or
liquid flow line to be attached and reattached without the use of tools.
However, there are two primary styles of “quick-release” fittings which have distinct differences in application. First: Push to Connect fittings are typically used for low-flow/pressure tubing applications. Second: Quick-connect fittings are used in higher pressure pneumatic, hydraulic, gas, steam and vacuum applications. Let’s take a closer look.
Push to Connect fittings are available in different materials and are selected based on the application and tube material. These fittings are typically made of:
ALUMINUM
BRASS
STAINLESS STEEL
COMPOSITE
NICKEL-PLATED BRASS
PLASTIC POLYMER
BRASS PEX
(CROSS-LINKED
POLYETHYLENE)
They are easy to assemble by simply pushing the tube into the fitting where it seals. The most common styles are also easy to disassemble by pushing a collar on the fitting to retract the grip and allow the tube to easily slip out. Other styles are more permanent, where the tubing must be twisted out, often damaging
the fitting.

Some manufacturers offer Push to Connect fittings along with Shut-off valves, to be used with polyethylene tubing designed for use with a wide range of industrial water treatment applications, including:
WATER PURIFICATION
REVERSE OSMOSIS
ICE MAKERS
BEVERAGE DISPENSING
VENDING & OCS
RECREATIONAL VEHICLES
MARINE
CAR WASHING SYSTEMS
The fittings, valves and tubing used in these applications are typically required to meet FDA compliant materials and are listed with NSF International Standards 51 and 61. For applications requiring FDA compliance, these components are manufactured in white polypropylene with food grade EPDM O-rings.
Other Push to Connect fittings are intended to work with brass, PEX or CPVC tubing or pipe. PEX is a cross-linked, high-density polyethylene. CPVC is chlorinated polyvinyl chloride, a particular type of a thermoplastic. The fittings grip the tube/pipe with a series of metal spurs inside the fittings that tightly grip the OD when they are inserted into the fitting sockets. An O-ring (typically Neoprene) or other flexible material inside the fitting makes a tight radial seal on the outside diameter of the tubing to prevent leakage. The tubing is usually a
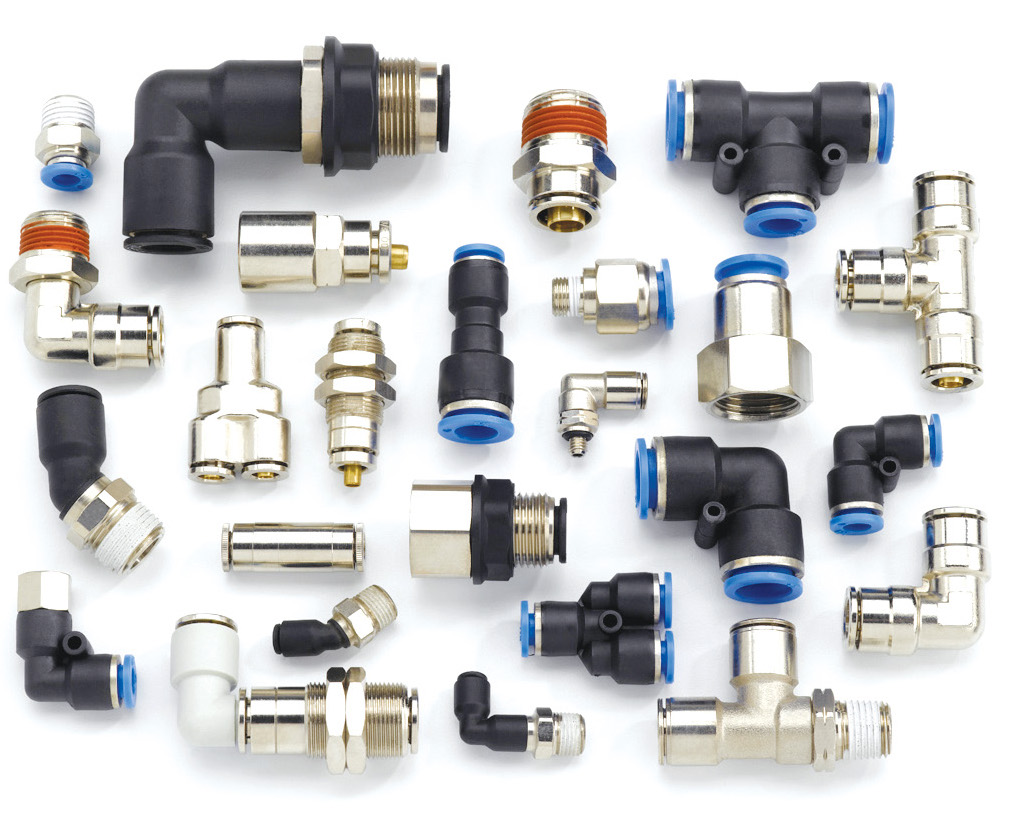
high durometer material such as a high durometer polyurethane
(i.e.95 shore A or higher), nylon, PEEK® or Teflon®. When these fittings are used with metallic tubing (i.e. brass), the tube OD may need to be grooved to accept the teeth of the fittings collet.
Fast and Repeatable
Push to Connect couplings allow for a fast and easy way to repeatedly connect and disconnect air or fluid lines. If a tube or hose in a fluid or air system needs to be disconnected and reconnected on a frequent basis, the best solution is a Push to Connect fitting. It will improve productivity, ensure a properly sealed connection and
eliminate downtime.
These fittings sometimes come as two components and have a poppet-style shutoff valve on each mating half. The shutoff, or check style valves, limit leakage during uncoupling and prevent air from entering the line when recoupling. They are also designed for minimum flow restriction, which minimizes pressure drop during
equipment operation.
One of the most critical applications for Push to Connect fittings is air break lines in tractor trailers that must meet Department of Transportation (D.O.T.) guidelines, which we will discuss later.
Not to be Mistaken with Quick-Connect Fittings
Though the terms Push to Connect and Quick-Connect are sometimes mistakenly used to mean the same thing, there are true distinctive differences. Quick-Connect fittings are two-piece, usually with self-sealing valves on each half that contain the fluid or gas when disconnected. These quick couplers are available in sets of male and female, or one half (a quick-connect plug) and in a variety of sizes and materials. Stainless steel and brass are the most common because of their corrosion resistance.
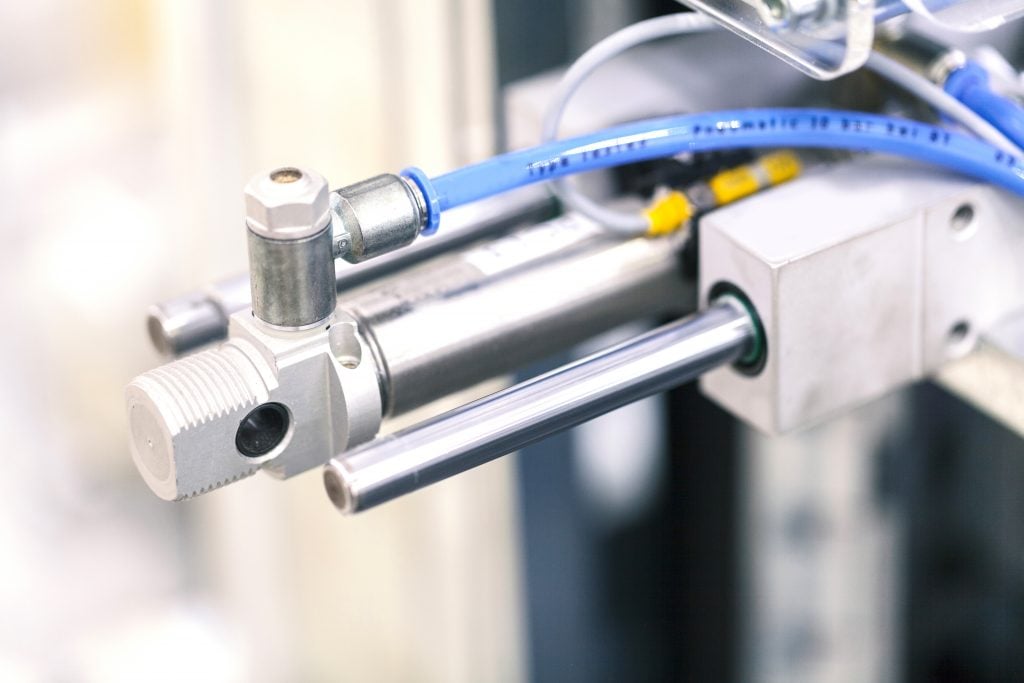
For some quick-connect applications, one end connection may be configured similarly to Push to Connect with easy assembly, simply pushing the tube into the fitting at one half by pulling the body backwards by hand, which then retracts onto the tube with a PTFE seal. The other half will have a compression fitting connection, or male or female NPT. More frequently, Quick-Connect fittings are used in high pressure applications, having a combination of compression and NPT male or female end connections.
The Benefits of Push to Connect Fittings
Push to Connect fittings are much easier to use compared to compression fittings. They are also more practical than permanent solvent-gluing CPVC and PVC pipes, or sweat-soldering brass pipes with a torch in general plumbing applications. These fittings have proven to provide highly reliable connections, even when they are hidden behind panels or other enclosed areas. When making joints for new installation or repair using brass tube, PEX or CPVC, Push to Connect fittings are the easiest and fastest method to provide an air or fluid tight seal when the tube or pipe is inserted.
1.
The ability to make a fast and reliable connection is the most significant benefit of Push to Connect fittings. Whether a new installation or an emergency repair, saving time is saving money.
2.
Unlike gluing or soldering, the tubing does not need not be completely dry.
3.
Push to Connect fittings are available in various materials, for different applications, to match the corresponding tube or pipe as stated above. (i.e. PCNB; Push to Connect Nickel-Plated or brass).
4.
They are easily detached for inserting new tubing or performing other maintenance.
5.
Push to Connect product lines cover many different styles, in a variety of sizes, for
multiple applications.
6.
Push to Connect fittings allow for easy connections without having to glue, solder, use clamps or compression style unions.
How to Use Most Push to Connect Fittings
1.
Remove burrs on the end of the pipe which can cut into the O-ring and make slight serrations where the fitting collar will slide on to allow for an adequate grip.
2.
Ensure that the Push to Connect fittings are recommended and approved for the application.
3.
Because there are so many types of these fittings, make sure to reference and follow the manufacturers’ instructions to ensure a tight seal.
4.
Some Push to Connects require a special tool to remove the fitting. The tool will typically come with the fitting, so be sure to use it instead of attempting to force it off the tube or pipe.
THE CHART BELOW OUTLINES THE FITTING SELECTION PROCESS BETWEEN PUSH TO CONNECT AND COMPRESSION FITTINGS:
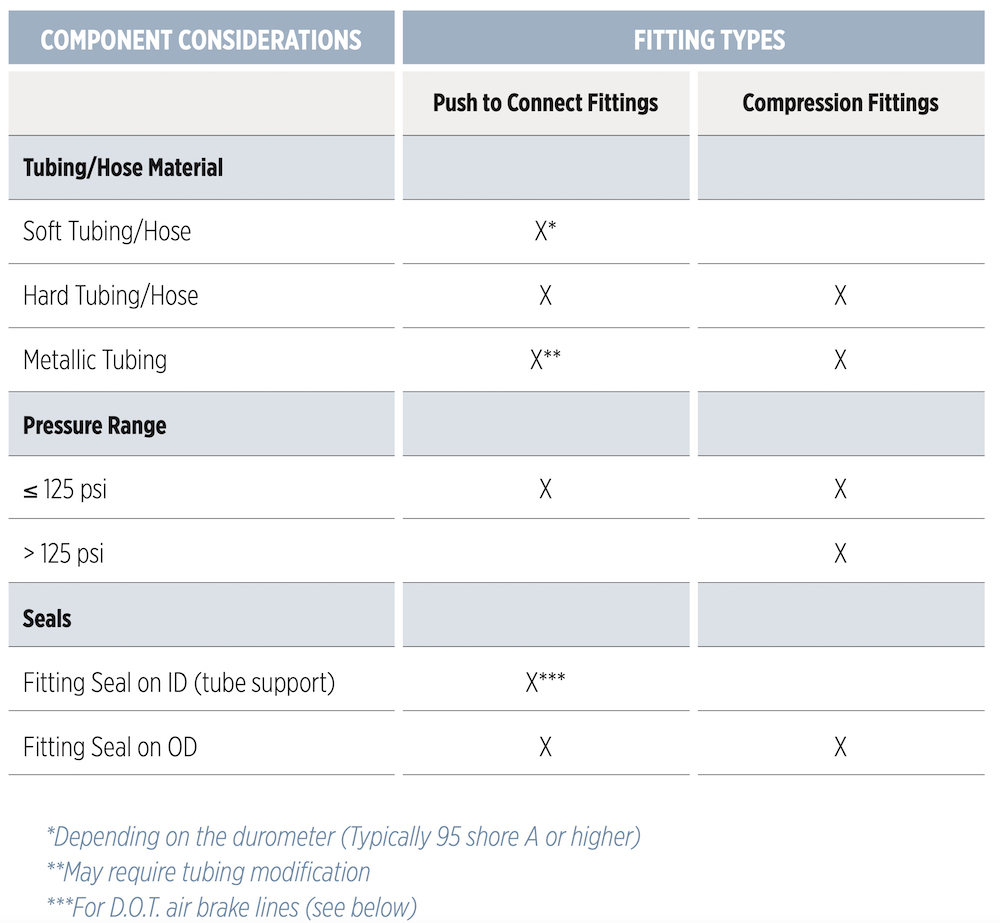
D.O.T Approved Push to Connect Fittings in Air Brake Lines
D.O.T. (Department of Transportation) approved Push to Connect fittings are the most commonly used connection in air brake applications. The compact style of a Push to Connect fitting is well suited for installing in confined areas. However, D.O.T. regulations require all nylon tubing air brake connections have fittings with an inner tube support. The tubing slides into the fitting and the metal inner tube support slides into the tube. This provides a more solid connection for over the road air brake systems.
Compression fittings are also suitable (and D.O.T approved) for many air brake applications and usually cost less than Push to Connect fittings, yet they are not as quick and easy to install, connect and reconnect. Quick installation, reduced maintenance and less chance of leakage makes up for the higher price of Push to Connect styles in most cases. Additionally, compression fittings must be installed with tools, which can be time consuming and more difficult in tight spaces. Where Push to Connect fittings are installed or removed easily without the use of tools, saving time and reducing the possibility of causing damage to surrounding components or equipment. The nut on a compression fitting must be turned to a specifically rated torque to ensure the proper seal, whereas a Push to Connect fitting does not have a compression nut. Instead, a leak free seal is achieved by easily pushing the fitting onto the tube or hose.
Compression fittings often need to be retightened to stop a leak. This can cause crimping or distortion of the tube, increasing the chance of future leaks. However, Push to Connect fittings rarely require adjusting after installation in order to remain leak free.
One advantage of some compression fittings is they can provide a higher pressure rating than the same size Push to Connect. Properly designed compression and Push to Connect fittings both meet or exceed D.O.T requirements. In order to ensure the proper fitting selection for a specific application, it is important to confirm:
· Required PSI pressure rating
· Type and material of tube/hose for
compatibility with the fitting
· Specific thread type (where applicable)
· For maintenance applications, refer to the owner’s manual for the specific application
Primary Specification of Air Brake Push to Connect Fittings for Tractor-Trailer Air Brake Systems
· Brass fitting with stainless steel tube support
· Compatible with SAE J844 Type A & B nylon tubing
· Features & Benefits: Quick installation, reduced maintenance and less chance of leakage
· Male pipe, female pipe, SAE straight thread
· Specified up to 250 PSI, temperature -40° F
· Meets SAE J2494 and D.O.T. FMVSS 571.106 air brake specifications for available sizes of 1/4″ to 1/2″. Stainless steel tube support for maximum flow for SAE J3494-3 requirements
Conclusion
Push to Connect fittings are utilized in most industries due to their ease of use, making fast, leak-free connections and disconnections. They also provide larger flow paths than barb style connections. Most Push to Connect are used in low pressure applications (up to 125 PSI), except in air brake lines that require up to 250 PSI, where specifically rated fittings are used.

Although simple in concept, many Push to Connect fittings are
engineered for specific applications. There are a wide variety of designs for specific, general industrial and commercial uses. It is imperative to select the right fitting (and fitting materials) for the application.
Two-part Push to Connect fittings have common components. Each has a style of plug and socket for their intended applications. The plug is the male half and the socket is the female half. When properly connected, the parts seal and lock the joint efficiently to maintain internal pressure and opposes tensile forces that may otherwise pull the joint apart. The two halves disconnect easily without tools, simply by unlocking and separating the two parts by hand.
For many common applications, Push to Connect fittings are the easiest to use, provide superior performance in tight spaces that are prohibitive to compression fittings and allow for the fastest installation, saving time and money.
SOURCES:
Hydraulics & Pneumatics
Beswick Engineering
Bendix Commercial Vehicles Systems, LLC
Brennan, Inc.: Versa Fittings
U.S. Department of Transportation: Federal Motor Carrier Safety Administration
Yukon Department of Highways and Public Works
The Spruce: All About Push-Fit Plumbing Fittings