
Historically, manufacturers own and operate a dedicated factory and develop or leverage existing supply chains to meet the needs of their customers. Consider a manufacturer located in Cincinnati, Ohio. They are in an ideal location for logistical distribution throughout the Midwestern and perhaps Southern United States. They have dozens of their own dedicated distributors and operate through other independent distributors. Traditionally this model has helped them to be a strong player in a large geographic footprint. Yet they find it difficult to be competitive in the Northeast or Western U.S., and prohibited from being competitive internationally.
Then, consider companies who have found opportunities to be competitive in a global market at local levels. To be effective, these companies leverage Distributed Manufacturing; a practice where a number of sister, partner or subsidiary factories serve their
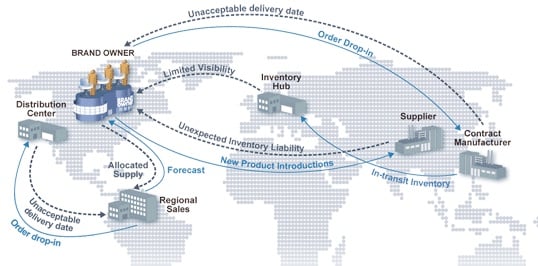
geographic distribution channels to create a highly agile supply chain. Advancements in information technology and interconnected ERP between locations allow these companies to operate as a cohesive unit, while being in tune with the needs of their regional markets.
This practice of distributed manufacturing in the industrial sector is becoming prevalent with innovative producers of everything from automotive components, appliances, hydraulic fittings, medical equipment and even nuts & bolts. Today many industrial companies are connected to the end user with multiple manufacturing locations and localized distribution channels, resulting in a united network that provides extremely high efficiencies at all levels of the organization.
Distributed manufacturing or sometimes called distributed production, cloud based producing or localized manufacturing, is a form of decentralized manufacturing practiced by companies using a network of geographically dispersed facilities that are coordinated using information technology. It is the manufacturing landscape of conversion from closed ended and restrictive to transparent and agile. It permits companies to access their supply chain locally with more flexibility, higher quality, faster service and lower costs.
Instead of relying on just a single headquarter location or third party overseas manufacturer; organizations that have evolved their business to a distributed manufacturing model are able to be more nimble in how they operate.
CONSIDER THE TWO MANUFACTURING
& DISTRIBUTION METHODS
Conventional Manufacturing
Consider XYZ Company located in Pittsburgh, Pennsylvania who makes valves used primarily in the oil & gas market and conducts conventional manufacturing and distribution methods. They employ leading engineers in the design and development of fluid handling products. They perform final assembly of their products at the Pittsburgh headquarters,

yet utilize subcontractors for parts and components located in the Asia. These subcontractors employ cheap labor to produce the valve components designed by engineers in Pittsburgh. The components are produced and then shipped to America where they are inspected and any out-of-spec product is rejected and returned. Without the control of localized manufacturing of all necessary components, the Pittsburgh valve manufacturer can incur more costs and slower lead times. This cuts into their margins and opens them for competitive intrusion. Add this to the fact that though there is a substantial O&G market in Pennsylvania and surrounding states, they are still competitively landlocked from the larger markets in the U.S. gulf region and overseas.
Distributed Manufacturing
Now let’s look at ABC Company who also makes valves for the oil & gas market located in Tulsa, Oklahoma whose market stretches down to the Gulf Coast, up to the North Atlantic and all the way to the Middle East. Beginning with a specialized project manager in Tulsa they identify a contracting firm to source engineers in local markets who are experienced in valves. These engineers repurpose the development of the company’s products to meet local needs in their remote markets. ABC Company then builds their own factories or develops relationships with dedicated manufactures near the end users who are capable of manufacturing their product to specification, meeting the same exacting quality standards and have or can easily develop a localized distribution network. The local design, manufacturing and logistics costs are much lower than performing all of these from Tulsa, providing better service for the end user and higher margins for the company. This distributed manufacturing method proves to be a very agile model that is flexible and scalable.
However, this is not a new concept. Take the example of General Motors and other domestic automotive OEMs. In the mid to late 20th century they all operated autonomous manufacturing plants, each assembling their own brands, such as

Pontiac, Oldsmobile, Chevy, Buck and Cadillac. There was some consolidation of engine manufacturing, but even body clips to join similar panels were different between brands. It wasn’t until foreign automakers such as Honda and Toyota began taking U.S. market share by opening plants in the U.S. did domestic OEMs begin to catch on to decentralizing and begin sharing their supply chains and engineering (decentralized to meet local demands). Furthermore, Japanese auto companies even took advantage of the U.S. domestic supply chain when they opened plants. U.S. Interstate 75 is the primary automotive corridor for OEMs and their supply chains. Running from Detroit to Miami, Route 75 is not only home to domestic car companies but also to Honda, Toyota, and Nissan, along with organizations such as Fuyao Automotive North America, a Chinese company with plants in Detroit and Dayton who supplies auto glass to the Route 75 supply chain.
Using a distributed manufacturing model takes advantage of regional and local resources that allow companies the ability to do revisions to the local customer’s specific product needs more quickly, leverages the local supply chain and decreases burdens on logistics.

A Distributed Manufacturing Model: Flexibility, Higher Quality & More Cost Effective
Implementing distributed manufacturing allows a company to take advantage of local resources and become leaner and more adept in product development for the particular region’s needs and get product to market much faster.
Being interconnected with local material and engineering resources, plus logistics and communications channels is integral to distributed manufacturing. Having close relationships with a local supply chain for everything from prototyping to component production gives an organization the ability to bring their products to market quickly and cost-effectively, which provides tremendous leverage over the competition.
In the current era of lean hardware development, small local manufacturers are integral to the success of distributed manufacturing.
Take the example of a high-volume manufacturer of fasteners to large OEMs. They can easily lose quality and have a high percentage of scrap simply due to the significant demands put on them and volume of product they are required to produce. They try to absorb these variables into their price, but when supplying such large industries these OEMs hold the buying power and set the price for the fastener manufacturer, leaving them with dangerously slim margins.
In the case of a smaller shop producing fasteners for machine builders, the MRO market or bridge building, volumes are lower and quality per part is more controllable. They have less scrap and can demand a higher comparative price. They may have far less revenue, but their profit margins can be significantly higher.
If we look to this second example as a model for distributed manufacturing consider how the leaner flexibility can be leveraged to produce higher quality parts faster and more efficiently and gain larger profits.
With less expenditure in capital equipment distributed manufacturing allows for less overhead and more controllable maintenance in operating fewer machines. When employing the expertise of smaller local suppliers a company can gain the efficiencies of those suppliers to produce components for the finished product.
Distributed Manufacturing Gives Control to the Parent Organization & Helps Local Economies
Localized manufactures with their own designers, manufacturing engineers and labor force create an interconnected eco- system that encourages development and growth of the local economy. This ultimately provides for Democratization of Technology by becoming more accessible to the local economy and its supply chain. New technologies and improved user experiences empower organizations to more readily access and use technological advancements in products and services.
These companies in the local economies are more connected and have the resources to be successful. It lowers the barrier to entry into the regional market and paves the way for distributed manufacturing to flourish.
The requirements of end users vary by region and are the overarching reasons for using distributed manufacturing. There are many inherent advantages to the manufacturer, which can include:
- More plentiful and less expensive raw materials in some regions
- Reduced labor costs from one region to another
- Lower logistics and transportation costs due to a close proximity to the end users
- More manageable distribution channels that are physically closer, providing the conduit between the manufacturing plant and end user
Inspiring Creativity and Increasing Motivation
Plants that are part of a decentralized network provide more independence for the local management. According to a study by Harvard University, decentralized manufacturing actually increases motivation and creativity by giving lower tier managers more responsibilities. When a manager is given a sense of ownership over an operation, efficiency increases among employees in both production and support positions.
Mangers at subsidiary plants typically have greater authority and autonomy when it comes to decision making. It can allow an entrepreneurial spirit to thrive by achieving results for their localized customers and provide a sense of ownership of their operation. This in turn increases efficiency among employees in engineering, production and sales. And because they have more authority to make decisions they are motivated to be creative in finding solutions and experiencing the immediate results of their efforts.
Increased Communication and Flexibility
If you can walk the talk, speak the language and integrate with the culture it is easier to communicate with a regional support network. The autonomy given to local mangers gives them more flexibility in their decisions without having to gain the blessing from corporate. Decisions that benefit the customer are made faster and product is distributed to customers more quickly. For instance, product manufactured in Nottingham, England can be delivered to London in one direction or Manchester in the other direction, both in less than two hours. Yet for instance, if that same product is coming from Cleveland, Ohio to Manchester it would travel as freight, likely change planes and be routed to a distributor once in England, only to arrive a few days after the order is placed (in the best case scenario). If there is any problem with the order, the cycle starts all over. Where in the case of the local manufacturer in Nottingham they could resolve any issues the same day. Reducing or eliminating any potential downtime at the customer.
Understanding the Customer's Needs
A decentralized organization can more easily relate to the local customer, receive more detailed, relevant and current information than a centralized company who it half a world away. A local marketing team can perform research that is relevant to their customers in order to identify their pain points and determine what features of product or supply will benefit them the most. Operating as a small business with the support of a larger corporate entity can be more responsive in meeting the needs of the customer.
These organizations operate multiple facilities that cover large areas with localized distribution, allowing products to be manufactured and distributed in defined geographic regions.
CONCLUSION: 6 REASONS FOR DISTRIBUTED MANUFACTURING
There are primary factors that prove the benefits of distributed manufacturing; production efficiencies, cost reductions, speed to market and quality control. The 6 reasons listed below are how these benefits can be achieved:
1. Manufacturing product closer to the end user reduces logistics cost and the time from production to sale.
2. Dependence on a single production facility can be risky. It is best to decentralize facilities and distribute resources from multiple suppliers
3. A manufacturer can be more effective when depending on and supporting multiple small regional economies.
4. Flexible financial commitment in facilities allows organizations to be more agile. When an organization is able to expand and contract their infrastructure they are in a better position to be competitive and withstand changes in economic conditions. Many organizations often run under capacity, especially in the U.S. This carries the burden of excessive overhead and wasted resources.
5. The time and investment to support larger production can be reduced when leveraging smaller facilities and utilizing local engineering, production and logistics experts.
6. Leveraging a broader localized network removes limitations such as cost and location of full time employees. Local engineering and labor is most likely to be much more efficient than a team separated by thousands of miles from the end result.
In today’s highly competitive landscape, large manufacturers must focus on the speed to market, increased efficiencies and consistent quality. We live and operate in a technologically connected world. Smaller and more responsive business units are more capable of managing high quality production at a local level than any time in history.
Sources:
Cerasis
Fictive
SME
HEARST
Industry Today