
O-ring face seal (ORFS) fittings are a highly popular and reliable choice in hydraulic and tube connections. Well designed ORFS connections provide a seal that is highly reliable due to its elastomeric seal and is one of the best choices for a leak-
free connection.
As the name implies, O-ring Face Seal (ORFS) fittings incorporate an O-ring at the face of the fitting and are designed to eliminate leaks in high pressure hydraulic systems.
Made to SAE J1453 standard, ORFS connections typically use Buna-N or Viton, 90 Durometer O-rings that seat into a grove in the face of the fitting. These
elastomeric seals provide a leak-proof, drop-in replacement for SAE 37° flared tube fittings, literally eliminating hydraulic leaks when used properly. When the connection is tightened the O-ring compresses against a flat face sleeve, which has been brazed onto the end of a tube. This makes a metal-to-metal seal with a leak barrier provided by the O-ring. The flat face sleeve also eliminates twisting of the tube and provides support during assembly.
O-ring face seal fittings can eliminate leaks in hydraulic systems at operating pressures as high as 6,000 PSI. They are designed specifically for applications where elastomeric seals are acceptable to overcome leakage and variations in assembly procedures. The fittings can be easily connected to a range of tubing grades by silver brazing. In addition, ORFS fittings can be disassembled and reassembled in the field to facilitate replacement of the O-ring or the entire assembly.
To ensure leak free connections, here are 5 things you should know about O-ring face seal fittings:
1. ORFS Fittings Help Prevent Component Failure
Many severe conditions can contribute to hydraulic component failure. Fittings and component assemblies are frequently required to work in very harsh environments, from corrosive off-shore applications to extreme heat and cold or frequent high pressure fluctuations.
O-ring face seal fittings are used in the majority of applications where there are very high pressures that are subject to flexing or pressure surges in construction
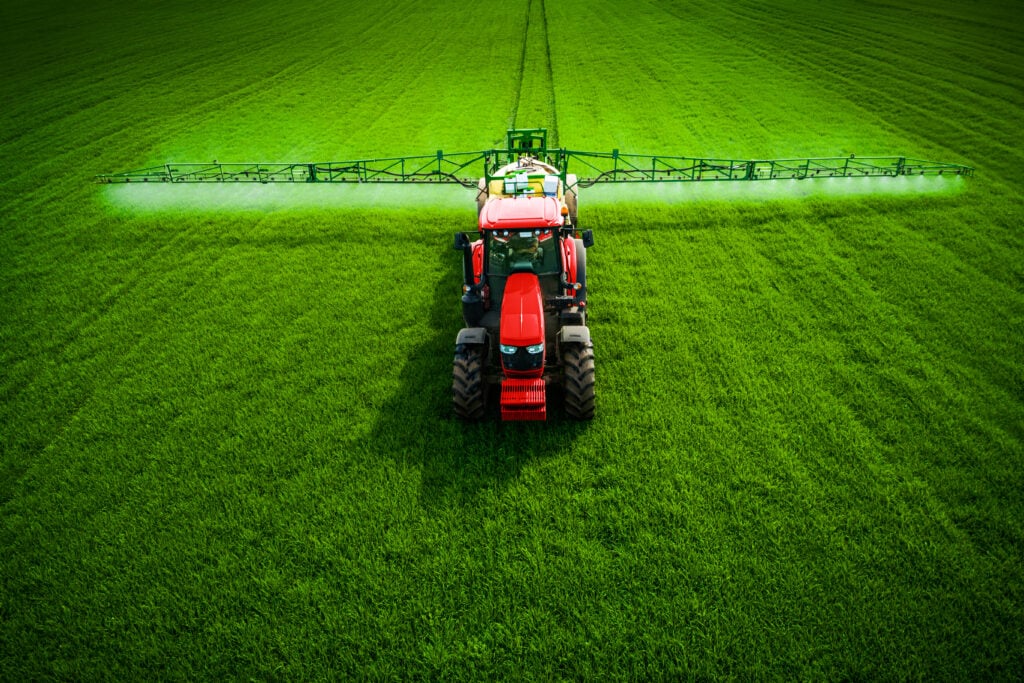
equipment, agricultural equipment, oil and gas, mining and the high performance industrial markets. They are also the preferred connection in high vibration systems because the soft O-ring seal absorbs shock better than any metal-to-metal sealed fittings. SAE J1453 ORFS fittings were first designed for off-road construction equipment and are now predominant in other transportation applications from CNG & LPG vehicles to material handling equipment and other industrial applications.
2. Causes of Hydraulic Systems Leakage
While hydraulic connections that incorporate an O-ring face seal are the most reliable against leakage, it can still happen. Yet the cause is rarely the fitting itself. The primary contributors to system leaks and how often they
occur include:
- Improper Installation: 60%
- Poor System Design: 20%
- Quality of Components: 15%
- System Abuse: 5%
While causes of leakage are usually distinguishable after the fact, the result can be costly. Not just to equipment and downtime, but the loss of fluid can be significant. Consider an operation running 24-hours-a-day and hydraulic oil at $25 per gallon, the cost of leaking fluid alone can add up:
- 1 drop every minute = 50 gallons per year = $1,250
- 1 drop every 10 seconds = 300 gallons per year = $7,500
- 1 drop every 5 seconds = 600 gallons per year = $15,000
- 1 drop every second = 3,000 gallons per year = $75,000
ORFS fittings are the best line of defense against costly fluid leaks.
3. Applications
O-ring face seal SAE J1453 fittings are popular in hydraulic lines onboard off road vehicles such as tractors, combines and other heavy equipment used in construction.
Due to the frequent vibration and actuation of
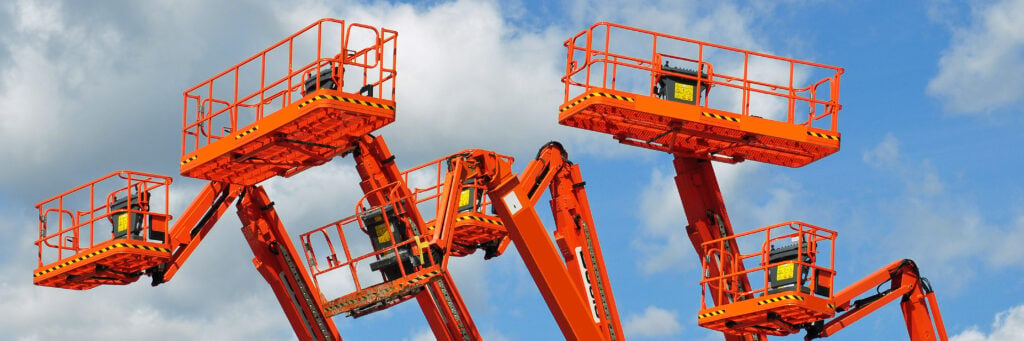
components in off-road vehicles, it is extremely important to reduce or eliminate the number of potential leak points and incidences of leakage. The SAE J1453 standard for ORFS fittings covers dimensions, threads, fitting and O-ring materials, and performance requirements of for use in hydraulic applications, as well as the interface of the O-ring face and nut portion of hose stem assembly.
A common, yet critical application for SAE J1453 ORFS fittings is with turbine flow meters in hydraulic fluid applications. A turbine flow meter is used for volumetric total flow and flow rate measurement. When the fluid flows through the meter it moves turbine blades that are free to rotate about an axis along the center line of the turbine housing, monitoring flow rate. Turbine flow meters play an important role in many hydraulic and pneumatic applications, including:
- Auxiliary systems in turbine hydraulic controls, liquid fuel
control systems, jacking/leveling and lube oil skids - Chemical plants
- Electrohydraulic controls (EHC)
- General industrial equipment
- Generators and transformers
- Hydraulic fracturing operations
- Lube auxiliary systems in hydroelectric plants
- Off-road construction and agricultural equipment
- Water treatment equipment
- Wellheads in oil and gas
- Wind power turbines
Flow meters that incorporate NPT end-fittings require adapters and can experience a number of leak points. However, units utilizing O-ring face seal fittings do not require adapters, need less space for meter installation and ensure fewer possible leak points.
Another important factor in many applications that use ORFS fittings versus traditional metal-seal fittings is that manufacturers can extend warranty periods in equipment because of the reduction of possible leak points.
4. System Design - Where it all Starts
System design is the first consideration for leak prevention in hydraulic systems. The right components must be selected to reduce the incidences of leaks and connection failures. Typically O-ring face seal fittings are the best or sometimes only practical choice. The following are attributes that should be taken in consideration when selecting system connections in the design phase.
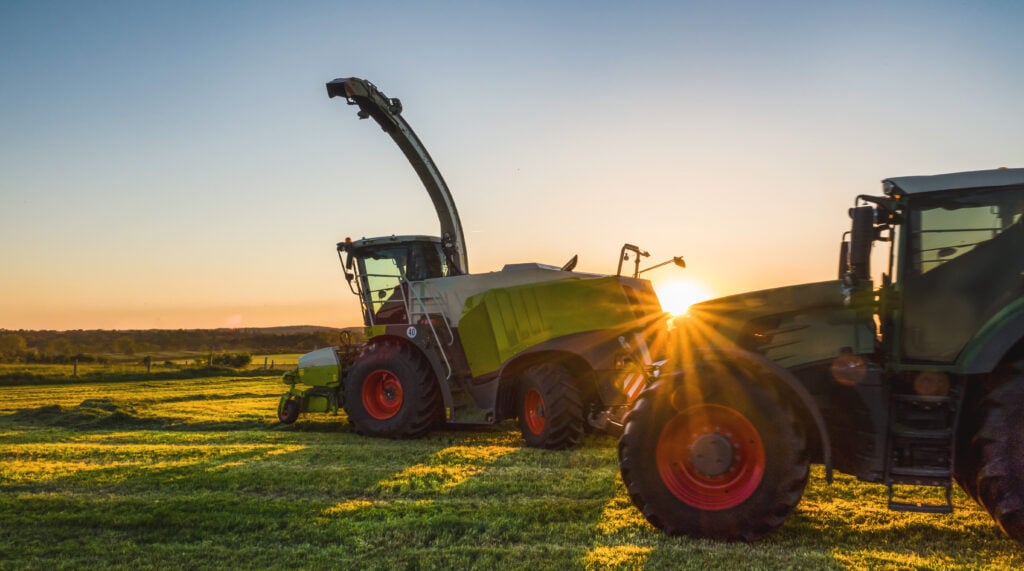
APPLICATION
The environment will determine fitting design and selection. The use of stainless steel or a protective coating on steel fittings extends the service life in corrosive environments. The most common finish for steel fittings is electroplated zinc to avoid rusting from the presence of oxygen, acidic gases and moisture. However, stainless steel is the best choice for highly corrosive environments such as off-shore or applications exposed to caustic chemicals. Finally the choice of O-ring material must meet the system conditions and application as well. A fluorocarbon or other material may need to be specified over Buna-N in certain applications, particularly in very high temperatures (see Temperature for Fittings & O-ring Seals chart below).
PRESSURE
The dynamic pressure rating of the fitting assembly is to be equal to or higher than the system pressure. Typically, fittings are rated at a 4:1 design ratio, which applies to normal operating conditions that can withstand moderate hydraulic and mechanical shock. For severe vibration and shock operating conditions a “de-rating factor” should be applied directly to the dynamic pressure of the fitting as shown in the table below:
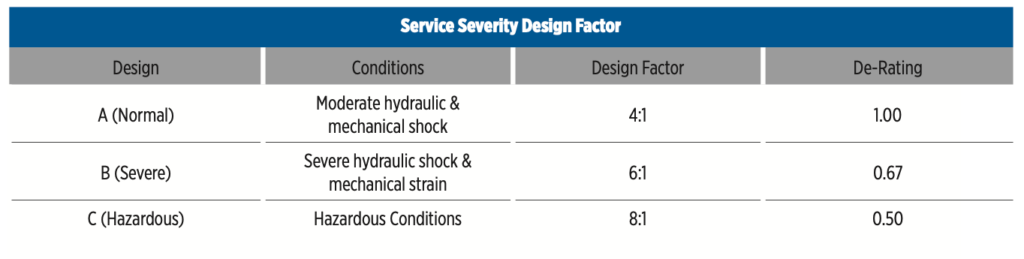
TEMPERATURE
The operating temperatures for fittings and O-ring seals are dependent on the metal material, plating and material of the seal. Temperature ranges for fittings and O-ring seal materials are shown in the table below:
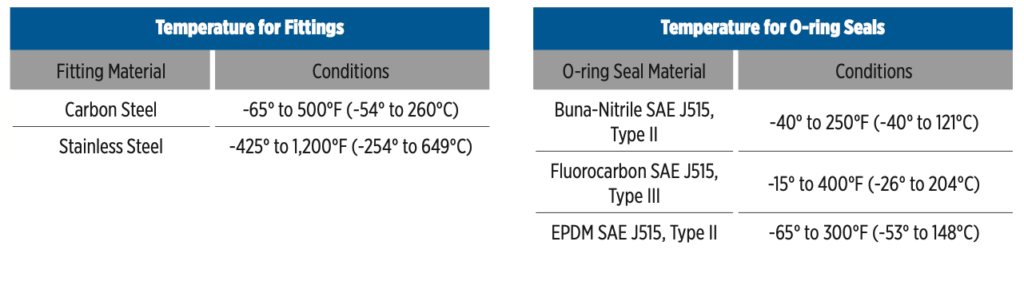
Other important considerations in system design that must be considered include:
- Contamination
- Environment
- Fluid velocities
- Media
- Shock
- Tube O.D. and Wall Thickness
- Vibration
5. O-Ring Face Seal Fitting Assembly Instructions
Proper assembly of the fittings is critical in all situations, but often in the field short cuts are taken that
can be a detriment to system performance. It is important to take the following steps:
FIRST: Inspect the fitting for possible contamination or damage that may have occurred in shipping or storage. Confirm the O-ring is properly installed into the groove in the fitting’s face.
SECOND: Using the system’s hydraulic fluid or a light lubricant, lubricate the threads and the O-ring.
THIRD: Have the face seal flange mated against the O-ring and finger tighten the flange nut.
FOURTH: Use the properly rated torque value to tighten the flange nut.
The above procedure is known as “wet torqueing”, which uses the system’s hydraulic fluid to lubricate the O-ring and fitting threads before installation. It is important to note that the coefficient of friction can vary significantly between assemblies because of differences in plating, material (stainless steel versus carbon steel) and thickness, as well as the thread quality between different components.
There is less torque required on the threads by lubricating prior to installation which produces a more consistent coefficient of friction, ultimately
increasing clamping force on the sealing area. Over tightening the fitting will make the threads deform and yield which will cause them to lose adequate clamping force or load on the seating area. Severe conditions and over extending operation of the system can cause additional yielding, resulting in unwanted leak points. If the fitting is not wet torqued it will compromise the efficiency and service life of the system. The table on the right shows the recommend torque values per tube and fitting size.
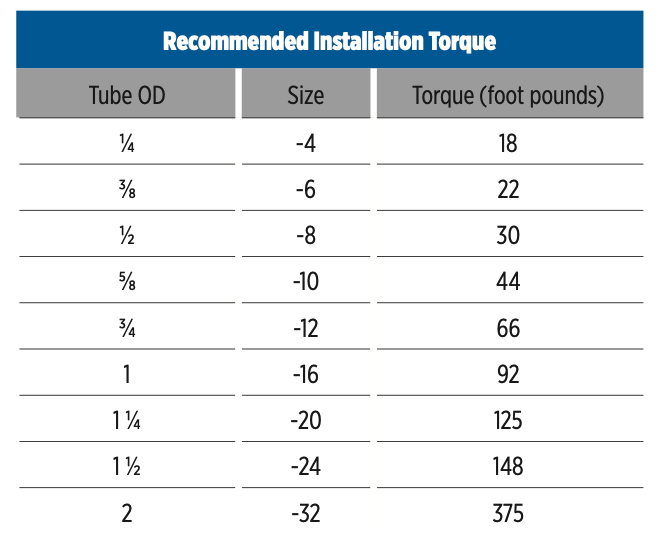
Conclusion
Standard O-ring face seal fittings and flat face sleeves are made from plated steel or stainless steel. However, custom-made stainless-steel O-ring face seal fittings and flange adapters are available for high extra corrosion resistance and proper sealing for critical and harsh-duty applications. These custom fittings are ideal in facilities alongside stainless steel instrumentation fittings and flareless bite-type fittings, as well as with other NPT and JIC products.
O-ring face seal fittings eliminate leaks in hydraulic and instrumentation systems, while permitting operating pressures as high as 6,000 PSI. Originally developed for hydraulic systems on both industrial and commercial equipment, they are the best solution in any application where elastomeric seals are acceptable for eliminating leakage and even variations in assembly procedures.
SOURCES:
Flow Technology
Hydraulics & Pneumatics
Mobile Hydraulic Tips
OEM Off-Highway
Pumps & Systems
SAE International
Windpower Engineering & Development