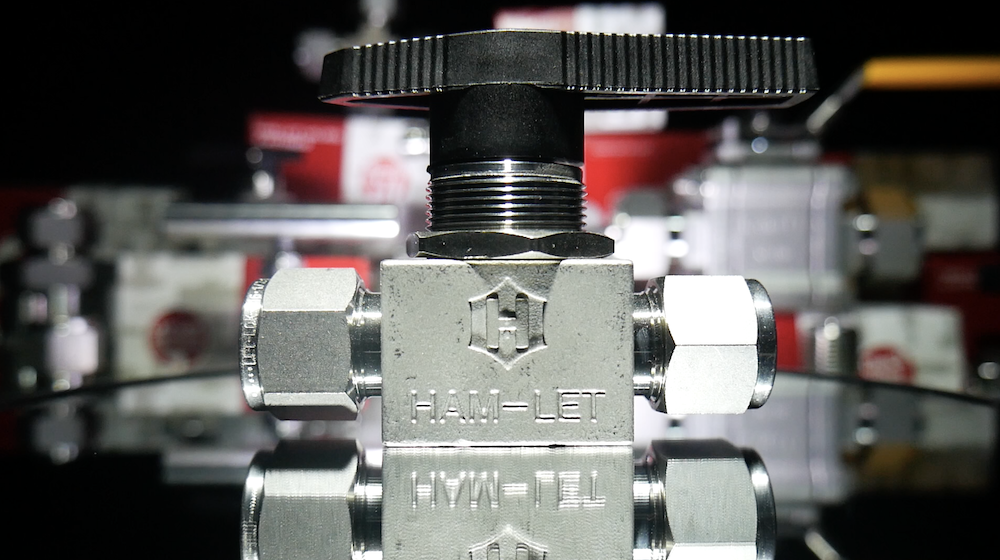
Evolution of Process Instrumentation Valves into the IoT Era
Process instrumentation is a collective term for a broad range of valves, fittings, gauges, sensors, and other components which act collectively for measurement and control to indicate and record physical attributes within the system.
As the basis of process control, the evolution of process instruments continues to improve the capabilities, repeatability, accuracy, reliability, and cost of process systems. These systems share a common need for flow, pressure, and temperature control. High performance components are required to satisfy the need for safe, reliable, and maintenance free equipment and long service life of the system.
Valve Types Used in Process Systems
Ball Valves are quarter-turn valve which use a hollow, pivoting ball (a.k.a. floating ball) to control flow through. It is open when the ball’s hole is in line with the flow and closed when it is pivoted 90-degrees by the valve handle. Ball valves are sometimes used to meter by closing the ball only part way, but not if a high degree of accuracy and control are required.
Bonnet Needle Valves make fine and precise adjustments in the amount of fluid or gas flow.
High Performance Actuated Ball Valves automatically generate torque that is transmitted to an output shaft which is connected to the valve’s stem rotating the valve’s ball in opening or closing the orifice to allow or block the media flow.
Plug Valves have a one piece top-entry design and are very similar to one piece top-entry ball valves. Plug valves (a.k.a. cock valves) are primarily used to increase or decrease flow, and for the distribution and change in the flow of media.
Toggle Valves allow the control of flow via a directional toggle switch. They are typically used in conditions where there are moderate pressures and/or temperatures.
Metering Valves are designed to provide metered stability and accuracy of flow rates in instrumentation, laboratory equipment and analyzers where accurate flow control is necessary.
Check Valves are one-way safety valves designed to prevent backflow. There is a backflow preventer which is held open by the forward flow. If the forward flow ceases and begins to backup, the preventer is held on the valve seat by a spring that is engaged by the back pressure, which in turn seals off backflow. Check valves are available in fixed or adjustable cracking pressure types, where the cracking pressure is the difference in pressure between the valve’s inlet and outlet ports.
Excess Flow Valves are similar to check valves. Excess flow valves incorporate a spring-loaded shut-off which will only close based on specified conditions when the flow through the valve exceeds a predetermined closing flow rate.
Relief Valves are designed to control a system’s pressure. Relief valves open in direct proportion to the increase in systems pressure, essentially releasing over pressure from the system, allowing the pressurized fluid or gas to flow from an auxiliary passage out of the system. In many applications of hazardous media, the lack of a relief valve may allow pressure to build up and cause damage to the system, or even fire or explosion.
Bleed Valves are used in process control applications to shut off the upstream pressure and bleed off excess fluid or pressure in the system. Bleed valves are either manually operated or controlled by an actuator.
Metering Ball Valves play an integral part in many process systems. They incorporate both metering and shut- off functions in one unit that combines an accurate micro-meter control mechanism for gases and liquids, along with a sealing device in a single unit. They are reliable and easy to operate and can drastically reduce the length of the line in the system. Metering ball valves are a single unit which can replace the need for two separate valves often used in a system, allowing for a decrease in installation and maintenance costs while reducing the risk of system flaws.
There are only a few metering ball valve styles on the market that provide highly engineered superior performance in exceedingly demanding applications. For instance, the Ham-Let® series won the Innovation Award from Flow Control Magazine for its novel technology solution for fluid handling applications in facilitating a more efficient flow control scheme, eliminating the need for multiple shut-off and metering devices in series.
This Shut-Off Metering Ball Valve Series delivers one of the industry’s highest degree of accurate metering flow for moderate pressure applications. It features an innovative and unique shut off capability which allows full control of the process from extra fine regulation to a complete valve shut off.

The choice of three precision stem tapers enables metering at flow capacities as low as Cv=0.0001 and up to 0.13, with up to 11 handle turns, meeting the high demand of precise flow control. In addition, the option of five O-ring materials provides the best temperature and chemical coverage and does not require packing adjustment, making it particularly ideal for the Oil & Gas analyzing industries and frequently used in system control panels with the inclusion of a panel nut.
Ham-Let twin ferrule valves and fittings are proven by TUV Tests, Lloyds Register, and others, to be intermixable and interchangeable with other leading brands.
Manifold Valves
Instrument manifold valves are a type of process connection system that connects one or more block or isolation valves which provide venting, isolation, and equalization for a variety of pressure measurement applications. Manifold valves provide a variety of functions in one device and are available in many different styles for specific applications. They consist of a combination of different valve types in one body having multiple connections. Manifold valves are used to support pressure instruments in measuring and equalizing pressures and maintaining differential pressures (difference in pressure between two given points). They operate in static, gauge, and variable in process instrumentation lines by blocking, bleeding, and calibrating pressure from the system.
VALVE PACKING
Most valves use some form of packing as a sealing mechanism to prevent leakage from the space between the stem and the bonnet.
There are two main types of valve packing materials. The most frequently used is PTFE (Teflon®) packing and is either pure material, or loaded with other materials such as silica, glass fiber, and carbon. Another popular valve packing is graphite, which can endure high temperatures of up to 1000°F (528°C).
Valve packing forms a seal between the valve parts and where the stem extends through the body, forming the seal between the internal parts of the valve and the outside of the stem. PTFE is the best material to use due to its superior fluid sealing capabilities, stem friction, and stem wear. PTFE is also quite resistant to attack from a wide variety of chemical substances.
In addition to leak prevention, valve packing protects valve stems and stuffing boxes from excess wear. The stuffing box (a.k.a. gland package) is the part of the assembly used to house the gland seal for preventing fluid leaks between sliding or turning parts of valve components.

Valve packing is compressed to avoid loss of fluid and damage to the stem. The packing must be tight enough to prevent leakage. However, if the packing is too tight it will impede the stem’s movement and possibly cause it to be damaged.
The proper choice of valve packing for the application prevents leaks, and protects valve stems from metal to metal contact, reducing wear. Instrumentation valve stem packing is used in any industry that requires liquid or gas transport and is required for efficient flow, metering and shut off in valves transporting water, chemical and corrosive media, particularly at high temperatures and pressures.
Valve packing can be replaced if worn, so it’s always advisable to keep valve stem packing in stock at all times to fix leaking valve stems when they occur.
Ensure Your Process Valves are IIoT-Ready
The industrial internet of things (IIoT) includes the interconnecting of devices such as instruments,
sensors, valves, and other components which are networked together via intelligent software in industrial applications. The connectivity of components provides a higher degree of automation which allows for the collection, exchange, and analysis of data improving productivity and efficiency while increasing system control and reducing costs. IIoT-enabled valves can identify and communicate data about the liquids or gasses that pass through them and the environmental conditions, such as temperature, humidity, and airflow.
There are billions of devices interconnected from what is essentially the IoT (Internet of Things) from high end industrial applications that can be controlled from one central system to common consumer products such as household appliances that can be controlled from your phone. However, on the industrial side,
IIoT is a significant part of conductivity in production operations. It is fundamental to acquiring data
from hundreds to thousands of process and equipment sensors which then transmits the data to central computerized controls via wireless or hardwired networks in order to cost effectively monitor every aspect of a system. Ultimately, enormous amounts of data are gathered and analyzed to locate and solve problems and maintain system control which reduces costs of maintenance and increases service life of components via a distributed control system (DCS).
INDUSTRIAL FLOW SYSTEMS
Industrial flow systems which include valves, fittings, and other components for control and transmission of gases and liquids in high-pressure and high-temperature pipelines, use cloud-based, open IIoT operating systems.
Some of the more advanced process instrumentation valve and fitting manufactures incorporate cloud- based technology into their products to increase reliability, reduce costs and minimize the physical space required for valve rigs. All of this opens new possibilities that were too expensive or too complex to implement in the past. The Industry 4.0 revolution which has provided IIoT gives the tools to move to digital systems and connect valves and other components to the cloud.

Previously, valves were only able to open and close manually. Today, IIoT valves can remotely sense the matter that passes through them, as well as various environmental conditions such a temperature, pressure, vibration, humidity, acoustics and more. Using a combination of machine learning, edge computing and the cloud, connected IoT process instrumentation valves provide customers with accurate and cost effective measurement and monitoring capabilities. Connecting valves to intelligent software controls allows device management, analytics and visualization never seen before, providing the display of parameters and historical data for each valve.
These IoT gateways can also be used to detect leaks, bursts, or deviations from normal operations in real-time through analytics. These technologies analyze data streams from the valves using machine learning models that run within a computer software execution environment through an open platform-as-a-service (PaaS) to create increasingly valuable solutions.
Safety and accuracy are top priorities when measuring and controlling temperature, pressure, level, and flow in a process system. The efficient measurement of these characteristics depends on functionality of components in the process instrumentation loop, from tap to transmitter. Transmitters are an important component in the system. They convert the digital signal produced by a sensor into a standardized instrumentation signal which is conveyed to a controlling or indicating device. The accurate readings of the transmitters depend on receiving accurate inputs of the vital components that feed results to the transmitter. Regardless of the efficiency provided by IIoT, the initial design and layout of a system is critical to the performance and accuracy of resultant measurements.
Additionally, with the ongoing skilled labor shortage in oil and gas operations, chemical plants, the pharmaceutical and food industries, and many others, leveraging this automation using sensors that are driven by industrial IoT predictive and self-learning systems has significantly increased productivity.

PROCESS & INSTRUMENTATION SOLTIONS: IOT SMART VALVES
IoT Smart Valves present a unique breakthrough in the process valves industry enabling online monitoring, control and management of various processes which allow immediate response for safety events, machine learning and optimization, along with machinery and equipment protection, device tracking and additional customer tailored benefits.
Industrial process valves are implemented in instrumentation and process lines in a wide range of applications. In order to measure pressure, temperature, flow, humidity, and indication of motion, one must use sensors and measuring devices.
Each of these external instruments are potential leak sources and most are not aligned with industry 4.0 applications and benefits. However, the unique Ham-Let’s IoTH-800 series delivers an innovative construct with advanced capabilities, providing a unique product line.
The IoTH-800 series is compatible with a wide range of industry 4.0 standards and is inter-operable with customer’s existing systems.
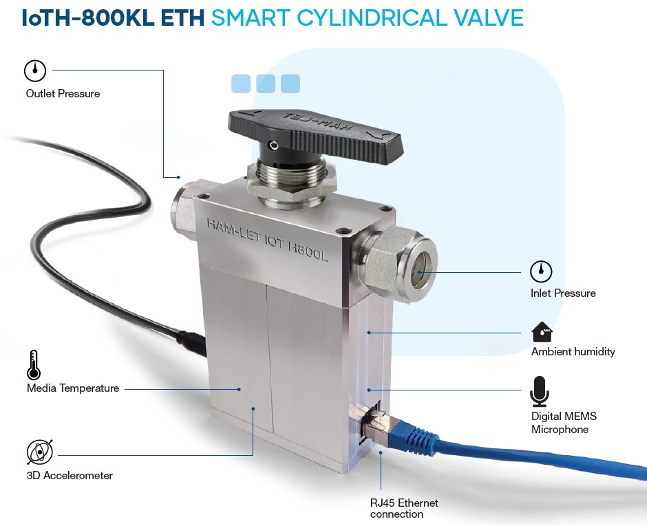
The IoTH-800 series features constant monitoring, management and control of motion indication, pressure, flow, humidity, and temperature measurement.
The IoTH-800 enables increased safety, reduced downtime costs, and improved system performance – providing valuable data with a lower total cost of ownership.
One of the IoT-H800’s exclusive benefits, is its ability to alert control systems when critical parameters are triggered.
Examples of triggered events include downstream pressure drops, temperature increases, leakage, and vibration. As an all in one product, the IoTH-800 smart valve provides the ability to predict these events and indicate when equipment maintenance is required.
The IoTH-800 series is offered in both wired and wireless configurations. Its applications, implementations and benefits are shown in the chart below:
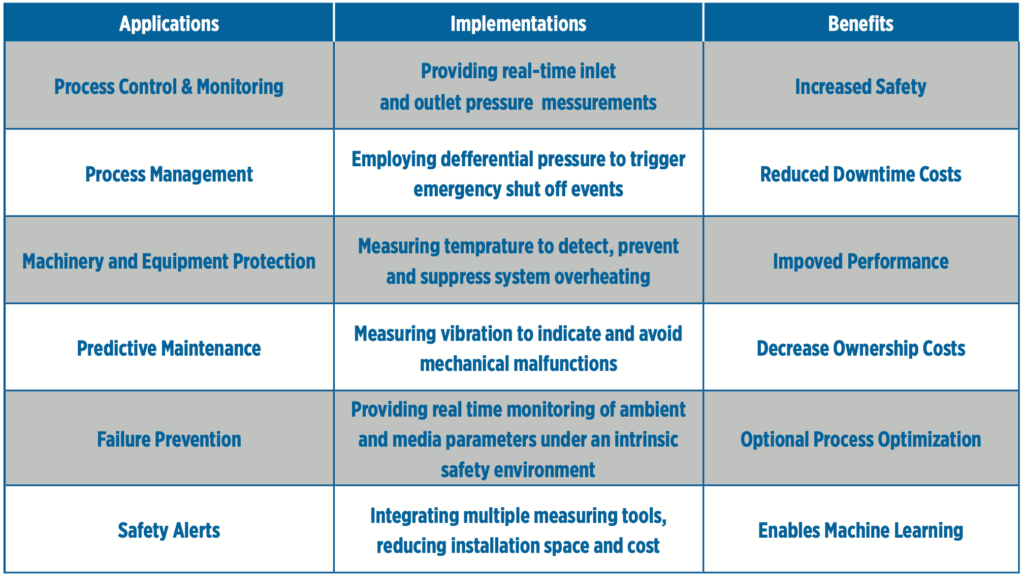
CONCLUSION
Process instrumentation control valves play a significant part in developing and maintaining an efficient process system. The features of a control valve must match the fluid requirements in the application to ensure stable flow control, ability to handle a range of flows, versatility, and connectivity for remote monitoring.
Instrumentation process control valves are available for wide variety of applications. They are used for controlling pressure, liquid level, liquid or gas flow or temperature in specific applications. Leveraging the Industrial Internet of Things (IIoT) there can be a

number of process valves in a system that work together
seamlessly to control and often automate processes. In addition, process control valves help the system use energy more efficiently and prevent the system from experiencing errors to ensure the application achieves the most desirable outcome in an efficient manner.
Determining the ideal valve for a specific application takes into consideration the media, valve material and purpose (such as metering, avoiding back pressure, adjusting flow, etc.). These factors along with system temperature, pressure, flow control and total system integration are the primary requirements in choosing the right valve for the application.
Sources:
Automation World
Cognizant
FTI Limited
Instrumentation Toolbox
Instrumentation Tools
International Society of Automation
Process Industry Informer
Process Technology Online
Processing Magazine
ThomasNet