Understanding the different thread types and sealing forms of hydraulic fittings is imperative. While there are many hydraulic fittings and connectors, there are standards for joining these products to pipe. This document will aid the understanding of what and where to use the most popular, such as BSP, JIC, thrust-wire and face seal connections.
BSP and NPT Thread Styles
The two most popular thread styles in the world are British Standard Pipe (BSP) and National Pipe Taper (NPT). They are the international standard for joining fittings and pipes. However, the difference between these thread styles is something to note.
BSP Threads
BSP is based on ISO 228 and Whitworth standard threads. BSP threads are among several technical standards that have been adopted internationally for interconnecting and sealing pipes and fittings.
The BSP standard incorporates Whitworth standard threads, which was developed in 1841 as the world’s first screw thread standard. Though it is among several technical standards for screw threads, it is extremely popular internationally for joining pipes and fittings.
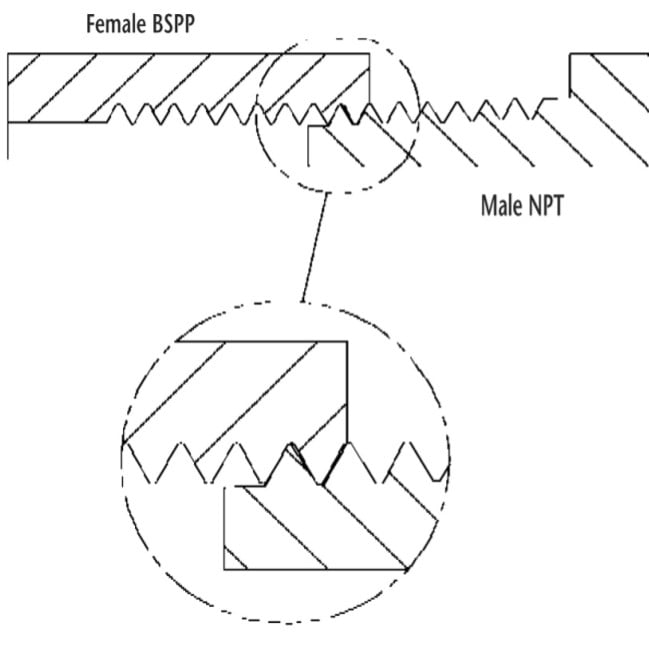
NPT Threads
NPT’s brethren is National Pipe Straight Mechanical (NPSM parallel threads), which are the U.S. standard for joining pipes and fittings. But while they are both standards for pipe threads, they are not interchangeable.
The Differences
BSP and NPT threads have more to do with where than what, which is an important distinction. Where NPT is prevalent in the U.S. and Canada, BSP is the primary standard in the UK, Europe, Asia, Australia, New Zealand, South Africa and many other countries. NPT and BSP threads are not interchangeable due to the differences in thread forms. NPT threads are pointed in the peaks and valleys, where BSPs are rounded. Most notably, the NPT thread angle is 60 degrees versus the BSP 55-degree angle. Though it has been tried, problems always arise when trying to thread a NPT male form into a BSPP female form. The dissimilar pitch will allow a misalignment of the threads, which causes leakage of fluid and even catastrophic failure under pressure.
BSPP Parallel and BSPT Tapered Threads
As stated, BSP threads are derived from British Standard Whitworth (BSW), which is an imperial-unit based screw thread standard. BSW threads were developed by Joseph Whitworth in 1841 and later adopted as a British standard. The Whitworth thread was the world’s first national screw thread standard, which gave wave to the vast popularity of BSP.
There are two types of BSP thread styles:
- BSP parallel threads
- BSP tapered threads
British parallel threads are often referred to as “G” threads, while British tapered threads are referred to as “R” threads. Each is measured in nominal sizes, and the threads are measured in threads per inch.
BSPP Parallel Thread Fittings and Adapters
British Standard Pipe (BSPP) parallel thread fittings and adapters are, by far, the most popular, with prominence in the UK, European, Asian, Australian, New Zealand and South African markets. Their popularity stems not only from being the first standard screw thread but also because of their excellent sealing properties and ease of installation. They are commonly seen on hose ends, adapters or ports when seated with O-rings or retaining rings.
These parallel thread fittings seal using a bonded ring. This bonded ring seal is pressed in-between the shoulder on the male fitting and the face of the female, creating a secure leak-tight seal. In addition, BSPP pressure gauges have a longer male thread and use a copper crush washer that is squeezed in-between the bottom of the male fitting and the bottom of the female BSPP bore hole, which forms a pressure-tight seal. The efficiency of seating with BSPP threads does not require thread sealants to form an excellent connection.
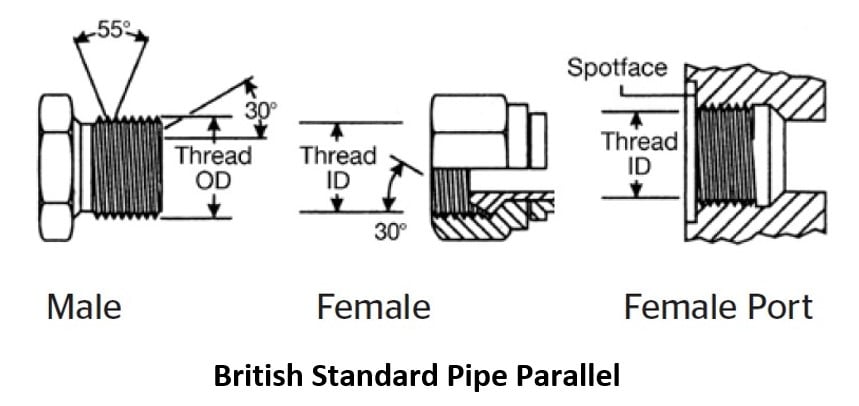
BSPT Fittings and Adapters
With a tapered thread, the fitting generally seals via metal-to-metal wedging of the threads. However, the seal is made with an O-ring or bonded washer. British Standard Pipe Tapered (BSPT) fittings and adapters are primarily for seating into a machined spot face, where a section of a workpiece is “faced” providing a smooth, flat, accurately located surface, often in a rough casting.
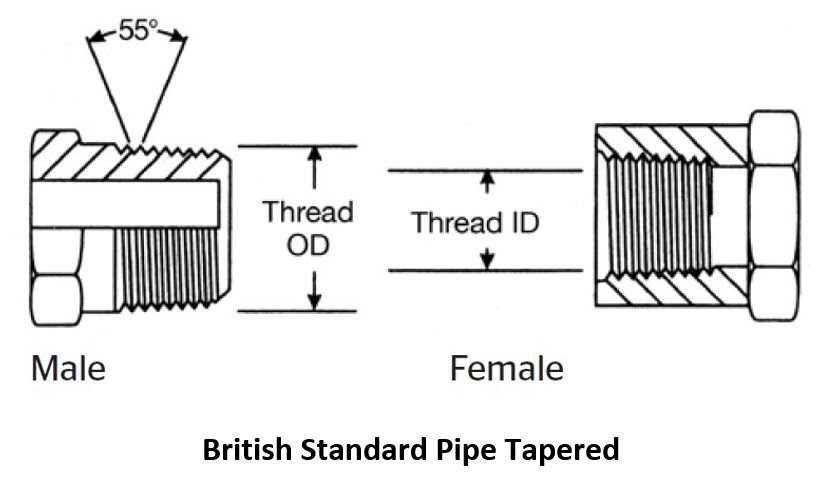
These fittings provide the best seal when assembled with a lubricant or sealant to form a pressure-tight joint. Both BSP thread styles are found in hydraulic applications from the oil and gas industry to heavy equipment and industrial machinery
BSP Adapter Pressure Ratings
The chart below represents design working pressures. Listed pressures are a guide and are not inrended as specification or standard ratings.
Note: adapter pressure ratings are applicable only to the size of the bore
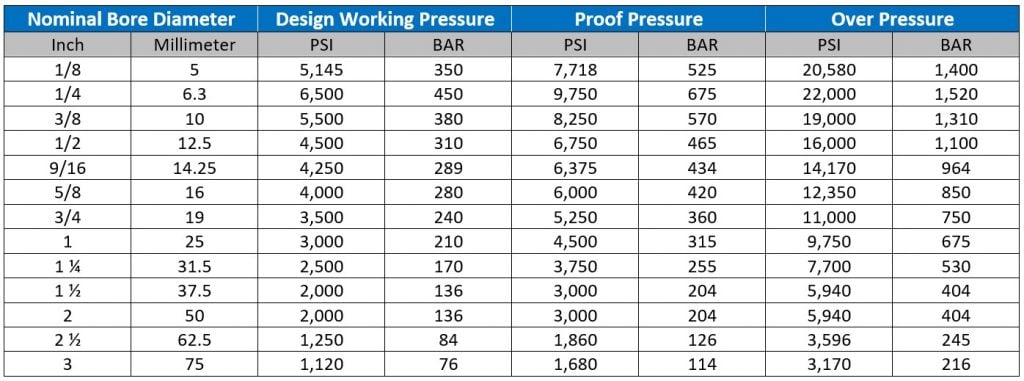
Working pressure is the ideal maximum pressure for the application. Proof pressure is the maximum pressure that may be applied to a device without changing its performance within the specification. Over pressure is the pressure where the device is most likely to burst.
As with other fitting types, BSP fittings have such a broad range of applications and are made from a wide variety of materials. In addition to steel, stainless steel, other alloys and brass, BSP thread-style fittings fulfill applications where the materials are cast iron, bronze or plastics, such as PTFE, PVC and nylon.
Thrust-Wire Fittings
Thrust wires are small, rigid wires inserted into holes in a nut or fitting, providing increased durability of the connection. Thrust-wire fittings are either BSP (8,000 PSI proof pressure) or JIC (6,000 PSI proof pressure) and are specifically used in high-pressure, high-vibration applications. These special fittings are some of the most robust and reliable on the market.
Though they are not as popular as many other fitting configurations due to additional installation steps, they are still very applicable where there is high vibration. They are manufactured from high-grade carbon or stainless steel, depending on the pressure and fluid or gas medium.
They are made with localized induction hardening for increased strength on surfaces that can experience high torque-stresses. This allows thrust-wire fittings to resist higher tightening torques and internal wear.
Regardless of their ability to withstand higher pressures, the thrust wires can be ejected from the assembly, potentially causing catastrophic failure. To safe-
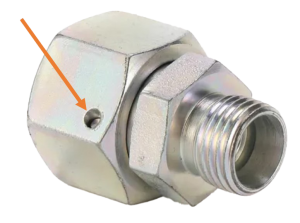
guard the assembly, after the thrust wire is inserted, the hole should be deformed to keep the wire from
slipping out under vibration.
Thrust-wire fittings are commonly found in construction, agricultural, oil and gas and mining equipment due to repeated vibration. They can also be highly effective in industrial equipment or any application where there is frequent actuation of the hose assembly, particularly under higher pressures.
Banjo Fittings
Banjo fittings are primarily used in low-pressure pneumatic applications. They consist of a hollow bolt and spherical union for fluid transfer. Their name comes from the shape of the fitting, which has a large circular section that is connected to a thinner pipe — somewhat like the shape of a banjo. Banjo fittings are typically made of carbon steel; yet, depending on the application, they may be made of other materials.
Unlike standard pipe fittings, banjo fittings do not have to be rotated relative to the host fitting. This reduces the potential of damaging the hose by twisting when turning the fitting into place, and it allows the direction of the pipe exit to be adjusted relative to the fitting, where the threads can then be tightened independently.
Common applications for banjo fittings include:
- Brake caliper connectors
- Carburetor connectors
- Hydraulic clutch systems
- Hydraulic power systems
- Power steering fluid connections
- Turbo charger oil feeds
- Variable valve timing systems
More recently, they are found in fuel dosing for Selective Catalytic Reduction (SCR) systems. SCR is an advanced active emissions control technology that injects a liquid-reductant agent into the exhaust stream of a diesel engine through a special catalyst. SCR technology is capable of achieving nitrogen oxide reductions by up to 90 percent.
AN Fittings
Army Navy (AN) is an Air Force-Navy aeronautical design standard for use in U.S. military aviation applications. AN fittings meet strict performance standards employed by the aerospace industry. Over time, AN fittings became popular with most U.S. military Original Equipment Manufacturers (OEMs) and contractors. They soon became popular in civilian applications, but they were often mistaken for the Society of Automotive Engineers (SAE) 37-degree fitting. By the mid-1900s, many sizes of 37-degree flare fittings became widely used in traditional industrial markets and was often confused with the AN standard, which created significant misconception in the market.
JIC Fittings
In an effort to elevate the confusion with the strict standards of AN fittings and to standardize across general manufacturing industries, the Joint Industrial Council (JIC) established specification standards for fittings. The most common being the JIC 37-degree fitting. This JIC specification has a marginally lower class of thread quality than military thread standards (i.e., AN fittings), yet is significantly less expensive and ideal for general applications.
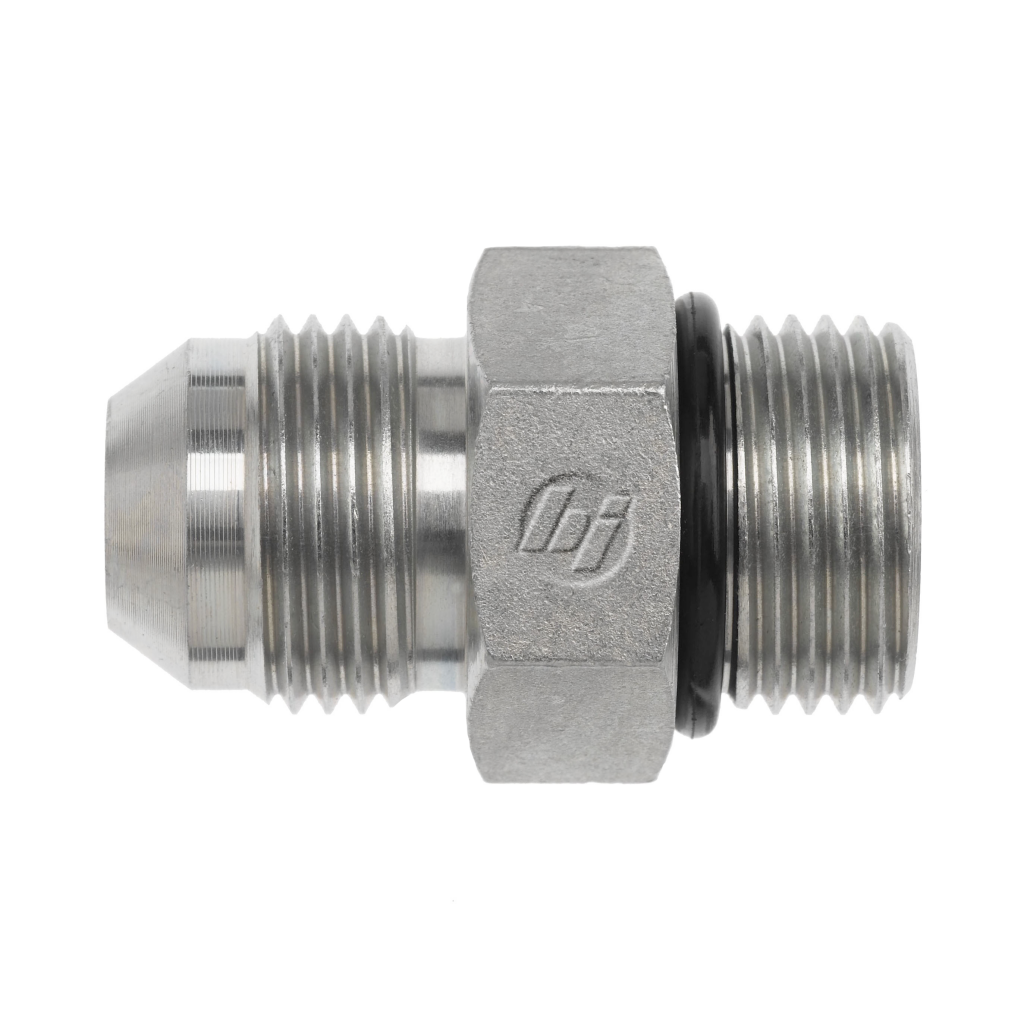
Subsequently, SAE adopted the JIC standard, as well. Today, JIC fittings are defined by the SAE J514 and MIL-DTL-18866 standards and are commonly fabricated from bar stock, forged carbon steel, forged stainless steel, forged brass, machined brass, Monel and nickel-copper alloys. These fittings are found in highpressure applications of up to 5,000 PSI in smaller bore diameters.
The majority of those involved in hydraulic applications agree that JIC (or SAE) 37-degree fittings are generally interchangeable with AN fittings. However, it is important to keep in mind that JIC fittings are not acceptable for military aviation or aerospace. JIC (or SAE) 37-degree fittings and adapters are intended for industrial, construction and agricultural equipment, as well as other heavy machinery material handling applications.
Hydraulic tube fittings made to J514/MIL-DTL-18866 include 37-degree flare seating face seal and 24-degree flareless type fittings. This is where the O-ring face seal (ORFS) fittings conform to SAE J1453 and ISO 8434-3. These specifications cover adapter unions, plugs and pipe fittings. J514 fittings and adapters are frequently made of steel for applications ranging from 1,500 to 6,000 PSI. These leak-resistant, full-flow connection fittings are used in a variety of hydraulic system applications, such as fuel delivery and fluid power applications.
ORFS Fittings
ORFS fittings are a highly popular and reliable choice in hydraulic and tube connections. An ORFS connection provides a seal that is extremely reliable due to its elastomeric O-ring seal. It is one of the best choices for a leakfree seal.
Designed to eliminate leaks in high-pressure hydraulic systems, ORFS fittings incorporate an O-ring at the face of the fitting, hence the name. Made to SAE J1453 standard, ORFS connections typically use Buna-N or Viton, 90 Durometer O-rings that seat into a grove in the face of the fitting. ORFS fittings provide a leak-proof, drop-in replacement for SAE 37-degree flared tube fitting, eliminating hydraulic leaks when used properly. When the connection is tightened, the O-ring compresses against a flat
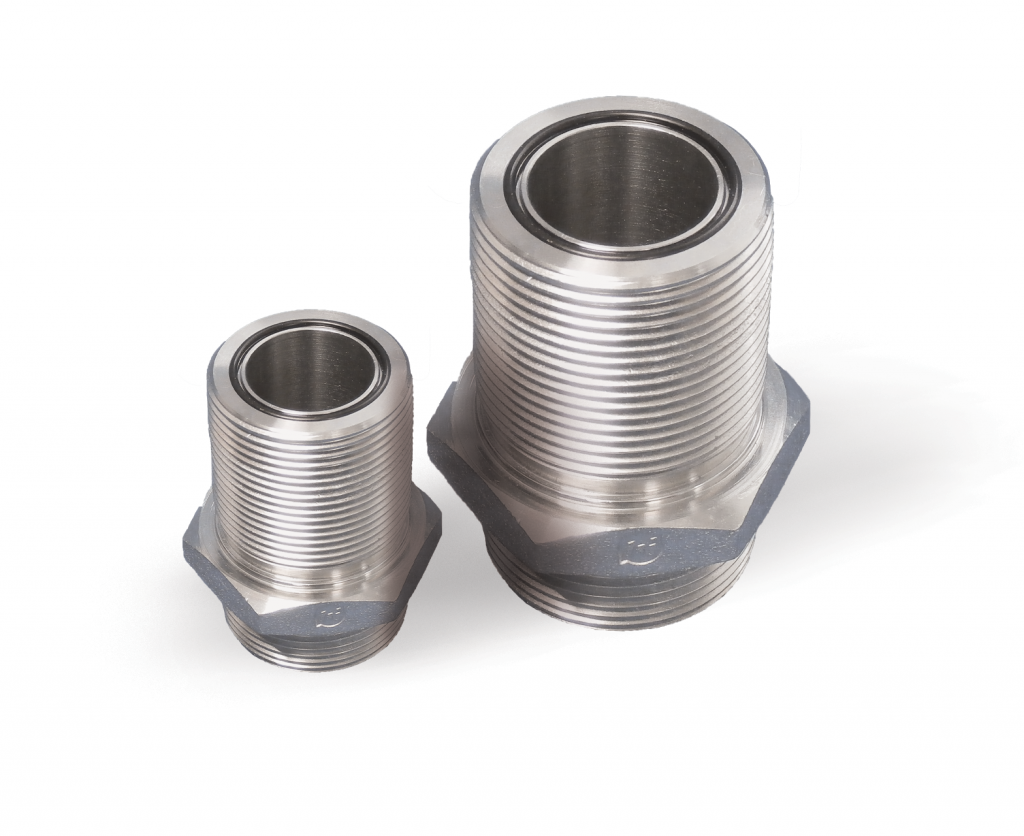
face sleeve, which has been brazed onto the end of a tube. This makes a metal-tometal seal with a leak barrier provided by the O-ring. The flat face sleeve design also eliminates twisting of the tube and provides support during assembly.
ORFS fittings eliminate leaks in hydraulic systems at operating pressures as high as 6,000 PSI. They are designed specifically for applications where elastomeric seals are acceptable to overcome leakage and variations in assembly procedures. The fittings are easily connected to a range of tubing grades by silver brazing. In addition, ORFS fittings can be readily disassembled and reassembled in the field to facilitate replacement of the O-ring or an entire assembly.
SAE J1453 ORFS fittings are a common choice in hydraulic lines for off-road heavy equipment and many other applications where there is a significant occurrence of vibration and frequent actuation of components. In these applications, it is important to reduce or eliminate the number of potential leak points. The SAE J1453 specification for ORFS fittings covers dimensions, threads, the fitting body and O-ring materials. It also covers performance requirements for use in hydraulic applications, as well as the interface of the O-ring face and nut portion of hose stem assemblies.
Many applications that use ORFS fittings versus metal-seal fittings allow manufacturers to extend warranty periods in equipment because of the reduction of possible leak points.
Conclusion
When using a popular thread style and sealing form, it comes down to location rather than which is better. For example, BSP and NPT threaded fittings are each highly efficient and reliable hydraulic fitting styles. While there are OEMs in America favoring NPT, there are other OEMs throughout the world incorporating BSP. Those OEMs that support international markets will utilize the most popular fitting style for that market. They do this not because it is necessarily a superior connection.
They do it for aftermarket maintenance purposes. Understanding BSP, JIC, thrust-wire and face seal applications are imperative for OEMs to truly serve their market. To learn more about the types of fittings Brennan offers, visit the university’s “Fittings 101” section to see all the styles.